Old Dutch Foods
Slipstick® Sanitary Horizontal Motion Conveyor Food Grade Conveying Equipment
The Slipstick Sanitary Conveyor, the first horizontal motion conveyor, is the food industry standard, recognized for its gentle, non-impact conveying motion and enviable record of low maintenance, high reliability and performance. Maintaining food safety and quality is the primary benefit of using the Slipstick in food processing applications. Unlike conventional vibrating conveyors that use a vertical pitching motion to propel material with repeated impacts which can cause the food to break or stick, the Slipstick’s single-drive mechanism provides a unique motion that glides the product down the pan, eliminating breakage problems for fragile foods such as chips, cookies, or cereal.
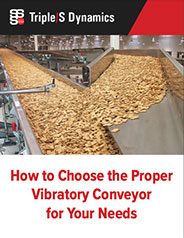
Free E-Book
Download our new E-Book to learn how to choose the proper vibratory conveyor!
Download the E-BookSanitary Vibratory Conveyor Systems
Food grade conveying systems for fragile food, snack food, and pet food / treats.
- Discourages build-up of materials on the surface
- Typically scours the pan clean so there’s less time required between production cycles for cleaning
- Exterior surfaces of the conveyor can be easily accessed for wipe down cleaning
- Cleaning under the conveyor is easier because typically there are no support frames or springs
- Mechanical simplicity over screws or drag conveyors.
- Requires significantly less maintenance.
- Safer conveying with no chains, screws, sprockets, rollers, idlers, or other moving parts located outside of the sealed and guarded drive unit
- Form / Function for Vibratory Conveyors
- Vibratory Conveyor Configurations
- Accumulation
- Food Grade Applications
Form / Function for Vibratory Conveyors
The key to horizontal motion conveying is the action of the conveyor upon the inertia of the conveyed materials. During the slow advance of the conveyor’s cycle, material is at a relative rest on the conveying surface. The quick return segment of the cycle gently slides the conveying surface under the material bed. Repeating this cycle 200 – 300 times per minute serves to smoothly convey the material up to forty feet per minute along the length of the conveying surface. Benefits of this motion include:
- Discourages build-up of materials on the surface
- Typically scours the pan clean so there’s less time required between production cycles for cleaning
- Exterior surfaces of the conveyor can be easily accessed for wipe down cleaning
- Cleaning under the conveyor is easier because typically there are no support frames or springs
- Mechanical simplicity over screws or drag conveyors.
- Requires significantly less maintenance.
- Safer conveying with no chains, screws, sprockets, rollers, idlers, or other moving parts located outside of the sealed and guarded drive unit
Based on its unique design that features a self-contained drive unit that has no outbound moving parts, the horizontal motion conveyor is virtually maintenance-free. Compared to conventional vibrating conveyors, powered by springs and convey material through impact on the conveyed material, the horizontal motion conveyor provides gentle transportation. And based on its relatively slow rotational speed, a typical drive unit will usually deliver more than ten years of life between service intervals, with only periodic lubrication required. Finally, since these conveyors utilize no springs or counterweights, they do not require the periodic tuning that is part of an ongoing maintenance program for conventional vibrating systems.
For materials that require transportation without compaction or segregation, the horizontal motion conveyor provides an ideal system. The “en masse” conveying method provided by the horizontal motion assures that mixtures will be delivered as originally blended, and fine particles will remain evenly distributed throughout the entire product bed – meaning retention of seasonings, coatings and breadings; prevention of oily fines build-up; and elimination of food product segregation.
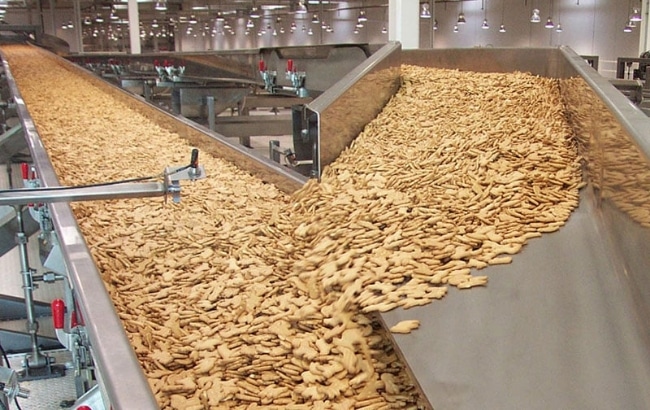
Vibratory Conveyor Configurations
Built in lengths from 4 ft. to more than 200 ft., the Slipstick offers a variable rate of product delivery depending upon the application, and is adjustable to suit most any requirement. Base mounted on the floor or suspended overhead, horizontal motion conveyors provide the level of versatility required for difficult installation applications. Conveyor drives may be positioned at either end of the conveyor, or mounted above or below. In addition, these conveyors can be operated at variable speeds, and their conveying direction is reversible. Conveying surfaces may be carbon, stainless, or abrasion resistant steel, as well as polyethylene plastic, or titanium.
The Slipstick can be suspended from overhead to maximize the use of valuable floor space or built with floor-mounted pedestals. Because it is dynamically self-balancing, no counterweights or heavy isolation bases are necessary. The drive module is mounted at either end or above or below the conveyor’s pan section.
Pan options for the Slipstick include multiple channels, pneumatically actuated discharge gates, and removable covers. Sealed tube sections provide added product protection and allow for CIP. The Slipstick can also be configured to align, singulate, divide, dry, or cool product as it flows through the conveyor.
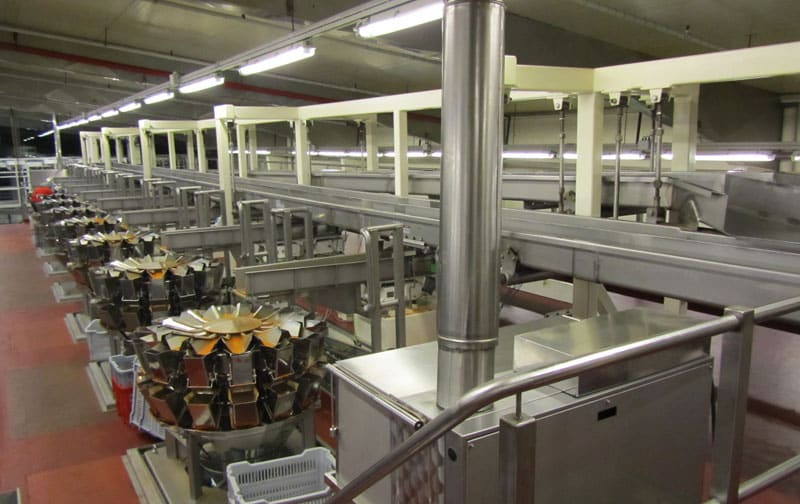
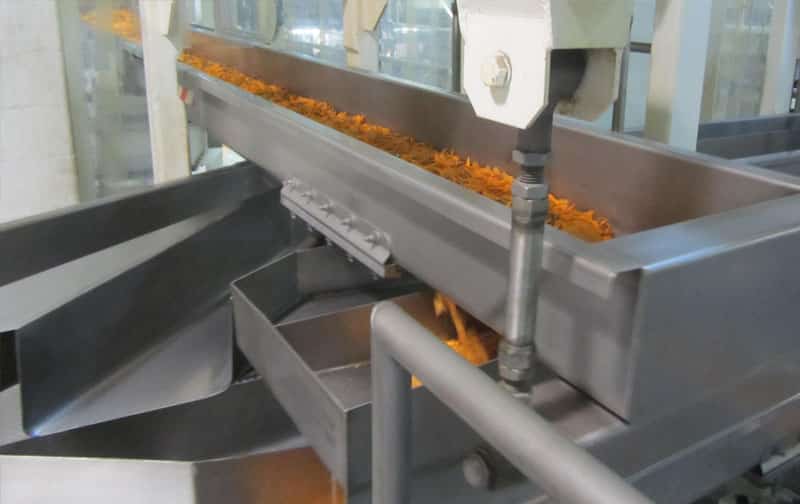
Accumulation
The Slipstick is a clear choice for in-line storage of many products. The one-piece seamless conveyor pan eliminates cracks, crevices and moving parts in the product stream. No carry-over from seasonings, coatings or powder residue to add to normal plant house-keeping tasks. This feature offers quick and thorough clean-out for enhanced sanitation and a greatly reduced risk of any cross contamination between product runs.
The gentle horizontal motion of the conveyor is uniquely suited for the storage and discharge of the most fragile products. There is no product stratification and it can be a sealed system if required, as well as controlled discharge or retention times of the stored product. By reducing the speed of the conveyor, the slower product travel rate will allow the product bed depth to build up within the conveyor trough. Accumulator product depth can be further increased by the use of stationary product dams positioned along the length of the conveyor behind. The gentle horizontal motion of the Slipstick Accumulator allows the product to build depth behind a pneumatically controlled stationary product dam without product damaging impact against the dam.
Product storage can be accomplished with the Accumulator style storage (greater product depths for shorter storage areas) with metered discharge options, long shallower bed depth conveyors that are regulated with conveyor speeds and the Slipstick loop system that consist of 2 conveyors in a parallel, circular product loop where product is bled off using singular or multiple gating options.
- Slipstick Accumulators can be equipped with pneumatically actuated product dams and level sensors to meter product to downstream equipment.
- Slipstick accumulating conveyors have been provided with storage capacities from as little as 20 cubic feet to over 1000 cubic feet. Capacities beyond these volumes are possible with the Slipstick Accumulator.
The system may be monitored by level sensors positioned above the product bed that can activate product dam position or to vary the speed of the conveyor for bed depth and discharge rate control. Another approach is the use of a distribution Slipstick conveyor mounted above the length of the accumulator equipped with closely spaced discharged gates that are actuated by level sensors positioned along the length of the conveyor. These are positioned to build product depth with a gentle product-on-product drop in order to build the maximum bed depth for large storage capacity requirements.
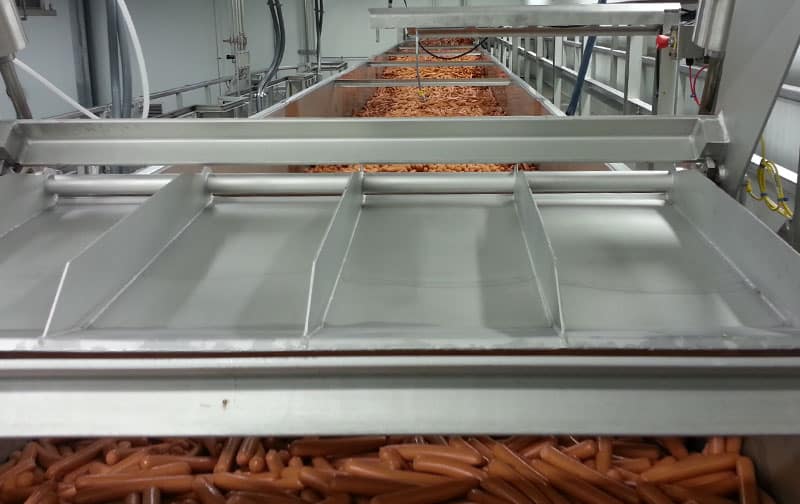
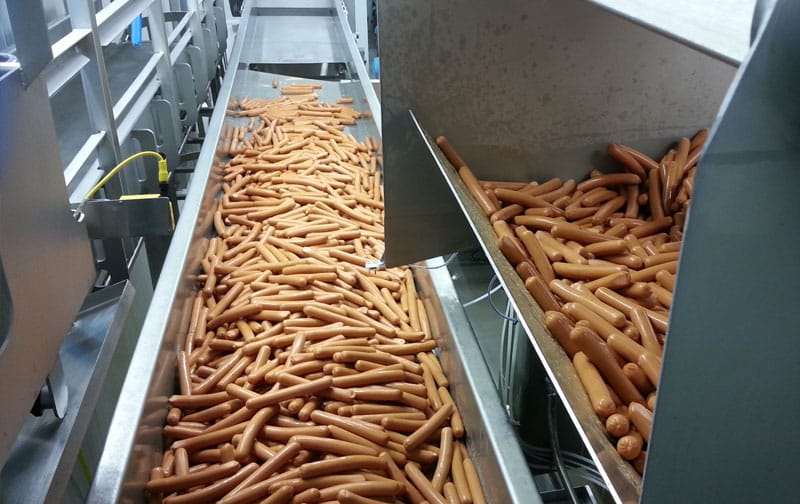
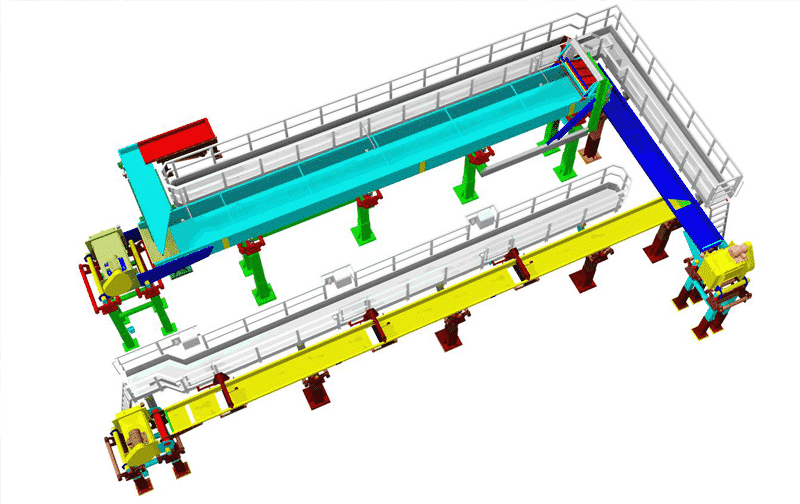
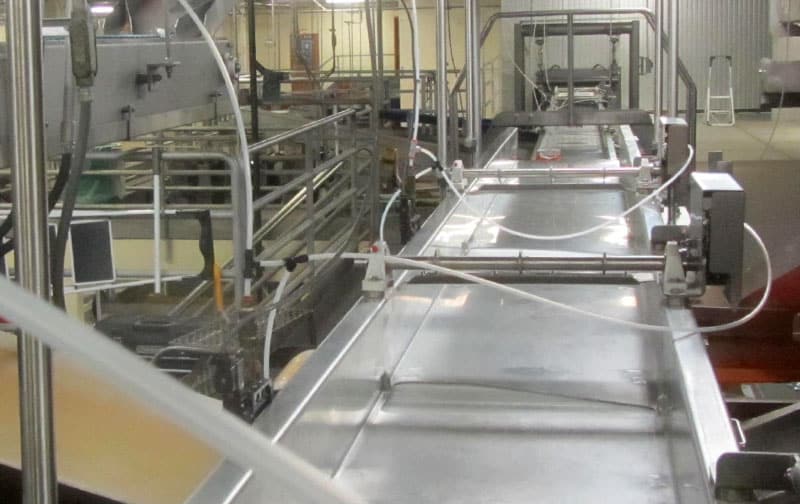
Food Grade Applications
Based on its many advantages over conventional conveyors, the Slipstick is currently being utilized conveying hundreds of different food products, including:
- Almonds
- Bacon
- Beans
- Candies
- Carrots
- Cereal
- Cinnamon
- Cocktail Sausages
- Cheese Snacks
- Chocolate Chips
- Cocoa Beans
- Coffee
- Cookies
- Corn Based Chips
- Crackers
- Grapes
- Marshmallows
- Milk Products (dry infant formula)
- Onion Rings
- Pasta
- Peanuts
- Pet Food/Treats
- Popcorn
- Pork Rinds
- Potato Chips
- Pretzels
- Raisins
- Shredded Cheese
- Trail Mix
- Wieners
Options
- Materials of Construction
- Impact liners
- Dual direction
- Supports
- Product dams
- Multi-lane
- Textured pans
- Chutes
- Flow Inhibitors
- Platforms
- Non-metallic sections
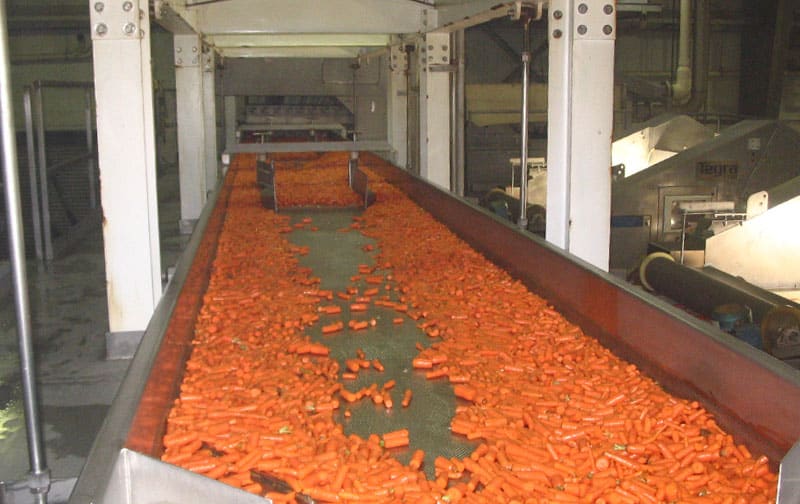
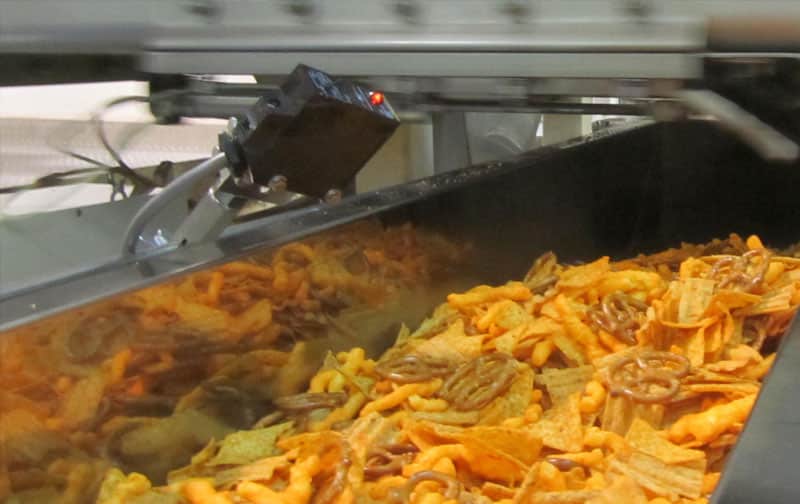
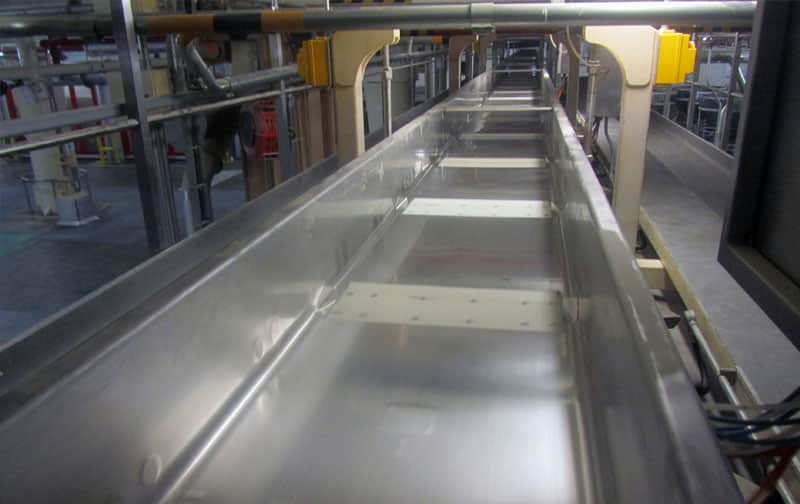