130 Years of Engineering History
A Humble Beginning
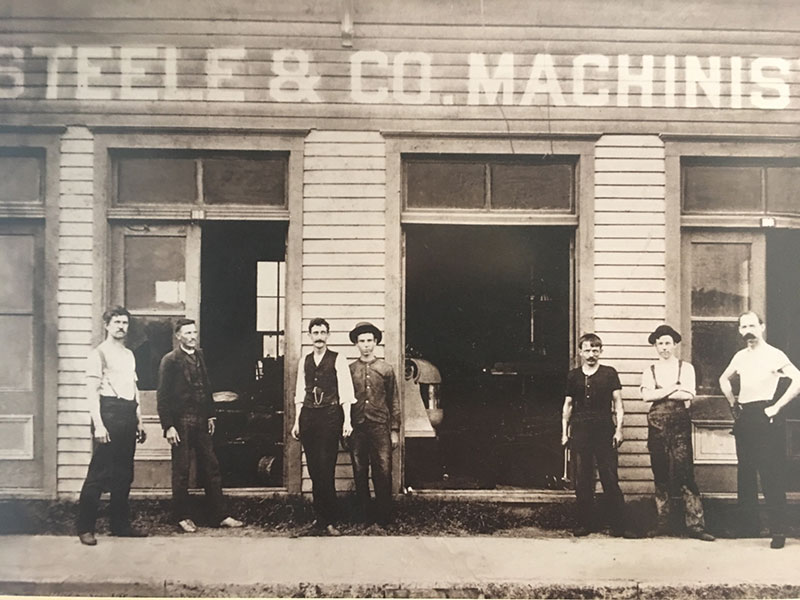
Earliest Shot of Walter & Henry
The history of Triple/S Dynamics is a long and winding road that started with Walter Livingstone Steele, born in Galveston in 1866, opened a machine shop sometime before 1888. When Walter met Henry Sutton, they incorporated as Sutton & Steele in 1888, the third manufacturing firm in the small city of Dallas, Texas, population at that time was about 10,000 according to the Texas Almanac.

Photo Texas Almanac ad. Caption: John F. Worley & Co. Dallas City Directory, 1902, book, 1902; Dallas, Texas. (texashistory.unt.edu/ark:/67531/metapth806910/: accessed April 23, 2018), University of North Texas Libraries, The Portal to Texas History, texashistory.unt.edu; crediting Dallas Public Library.
This early machine shop built some of the first enclosed DC motors and generators until a chance encounter with a customer who spoke of mining and gold.
By the time AC power had begun to replace direct current in the early 1900's, the young company had already begun to turn its attention to the new challenge of inventing and developing equipment to concentrate gold and other metallic ores without using water. Henry Sutton, the principal inventor, was granted dozens of patents on dry concentrating methods that used static electricity, air, vibration and combinations of the three to accomplish their purpose. The course of the company's future was forever changed.
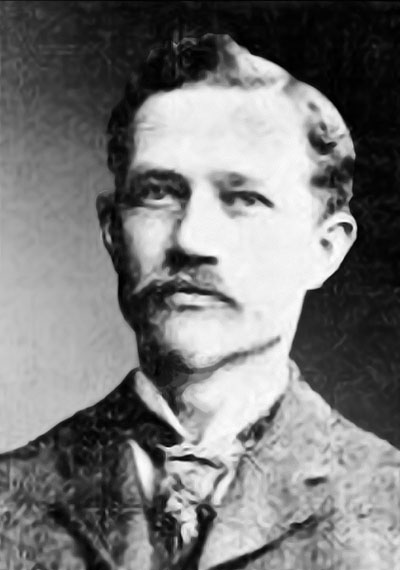
Photo of Gustave from Salt Lake City paper - 1904
At the same time, Gustave Overstrom patents a dry concentrating table. Overstorm, a professor of mining engineering at the University of Utah, also starts an engineering business designing mining machinery. Overstrom, a prolific inventor, patents the high-speed two-bearing inclined vibrating screen, licensing many patents to early manufacturers of industrial and mining machinery including Sutton Steele & Steele. The line between the two companies begins.
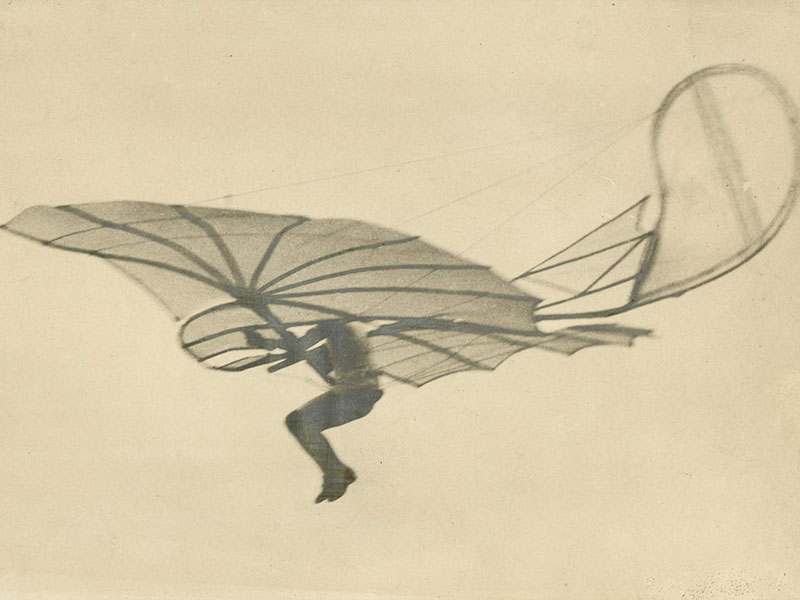
Photograph from the National Air & Space Museum
Edwin Steele, a Dallas young man, like many another young man, has found work very slack this summer and fall; but, instead of turning political agitator, he has devoted his leisure to science, on the line of the flying machine, and has about perfected and completed a device, which he believes, will solve the long vexed problem of aerial navigation. He has used for his shop in the construction of his machine, the rear of Sutton & Steele's machine shop, on Camp street, the latter member of the firm being his brother.
In 1896, Walter's younger brother, Edwin G. Steele, 22 years old was the subject of an article in the Dallas Daily Times Herald dated July 31, 1896 titled "A Dallas Genius about to Solve the Problem.”
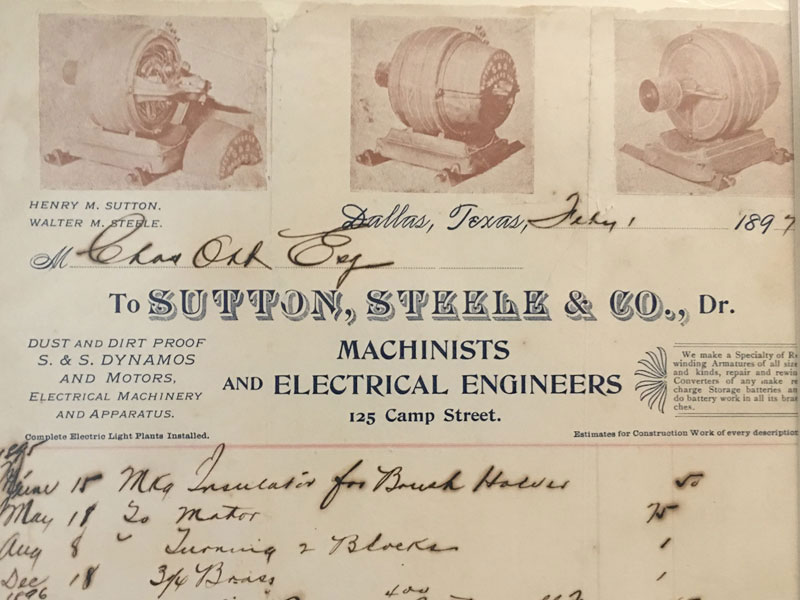
1897 Bill of Sale
The photograph is an original hand-written bill of sale from 1897. On the left side of the document, printed on the invoice it says "S & S Dynamos", an obvious precursor to Triple/S Dynamics name change 71 years later (just kidding, generators were called dynamos in 1897).
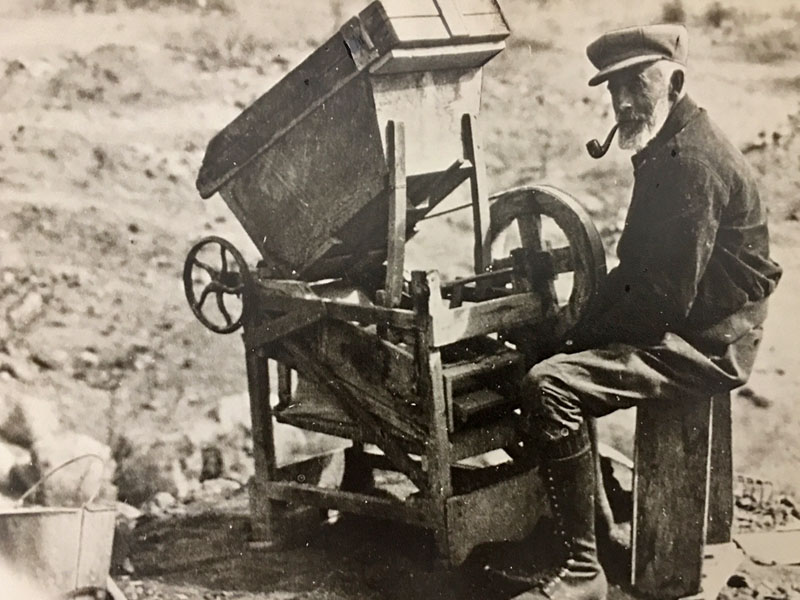
Original dry concetrators were made of wood - 1900
In 1900, Edwin becomes the second Steele to be a part of the growing business and the name is changed to Sutton Steele & Steele. The dry concentrators for use in the booming mining industries begins to sell. The first machines were made entirely out of wood.
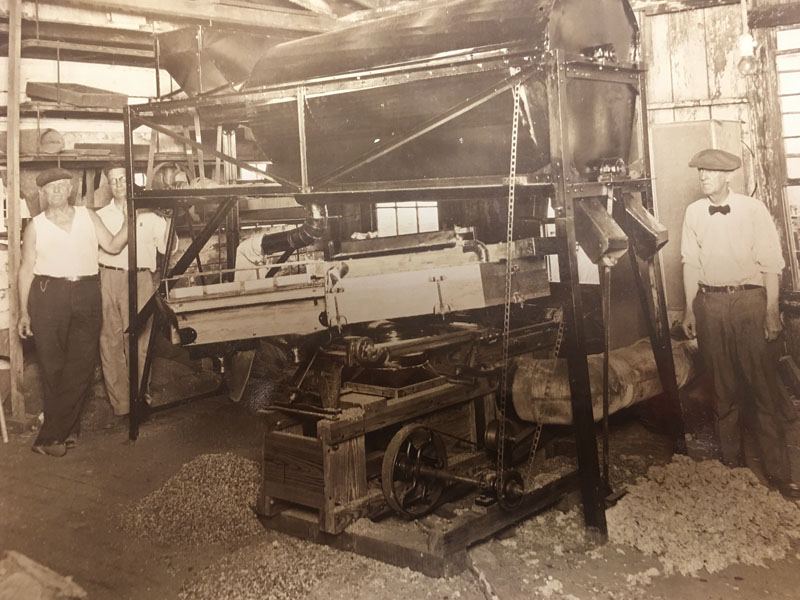
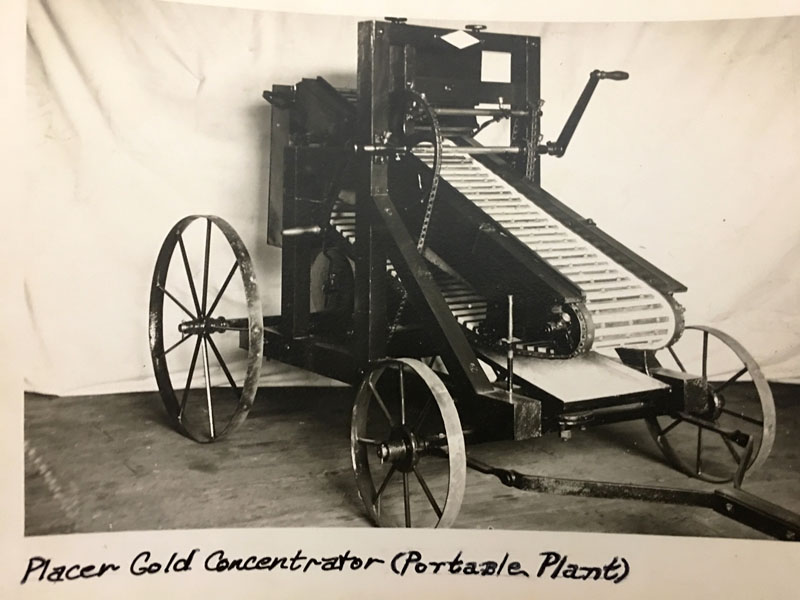
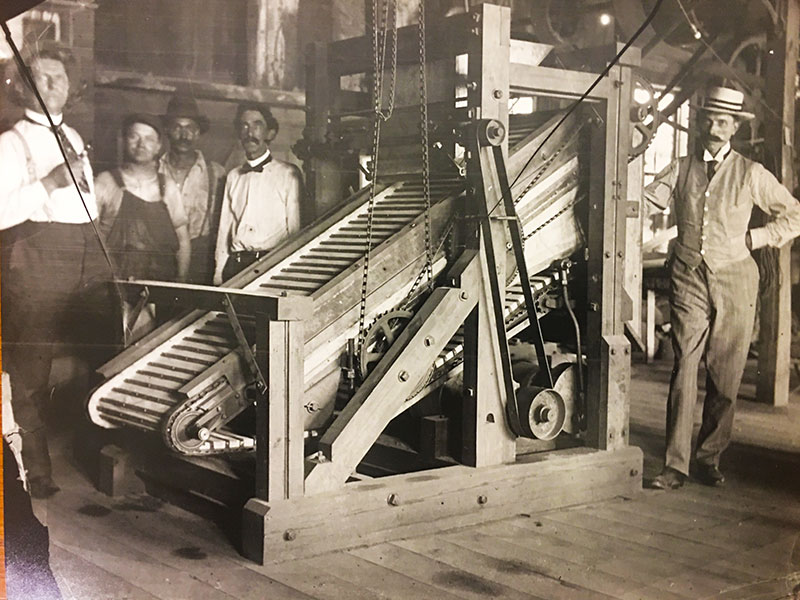
For the first decade of the 20th century, the young company is written about in magazines and newspapers around the country. The founders continued to perfect this dry concentrator along with a few other type of equipment.
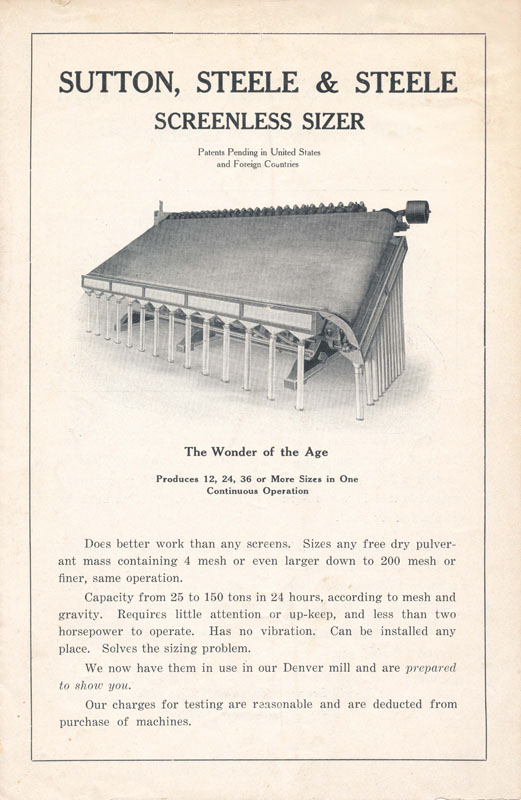
"The Wonder of the Age," 1914 - Download Brochure
“The Wonder of the Age” was published in 1914. The brochure states “Produces 12, 24, 36 or more sizes in one continuous operation”. The Brochure also discusses a demonstration test lab to be built in Denver Colorado. This is the oldest piece of printed literature we have in the archive.
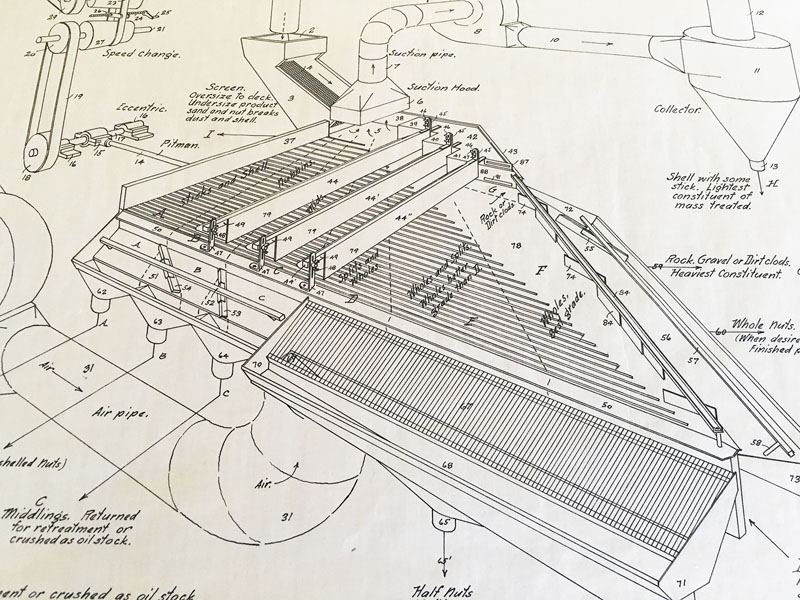


By 1919, Sutton Steele & Steele dry concentrators were installed in every state in the U.S. except Maine. The company also had installations in thirteen countries abroad. The first patent application drawn by Edwin was in 1919. Those original vellum hand-drawings are in our offices today. The plant officially moved into its new facilities exactly where we are today.
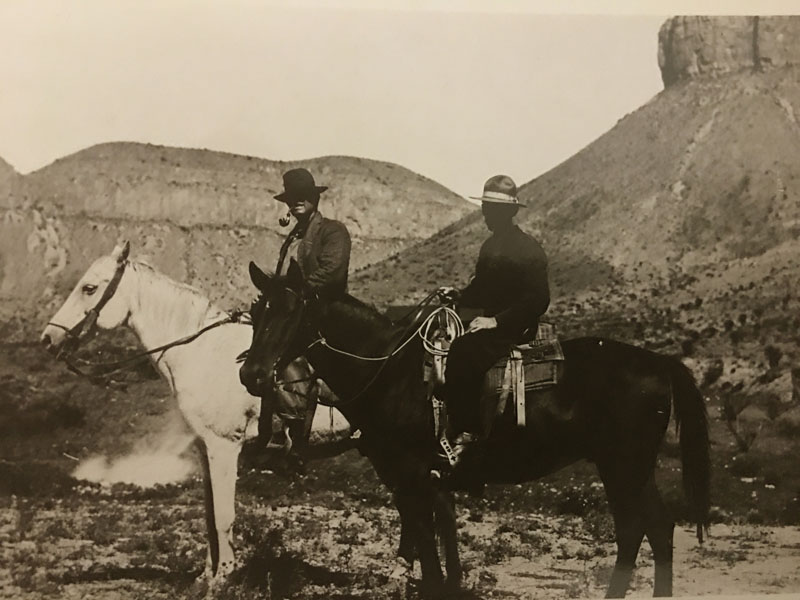
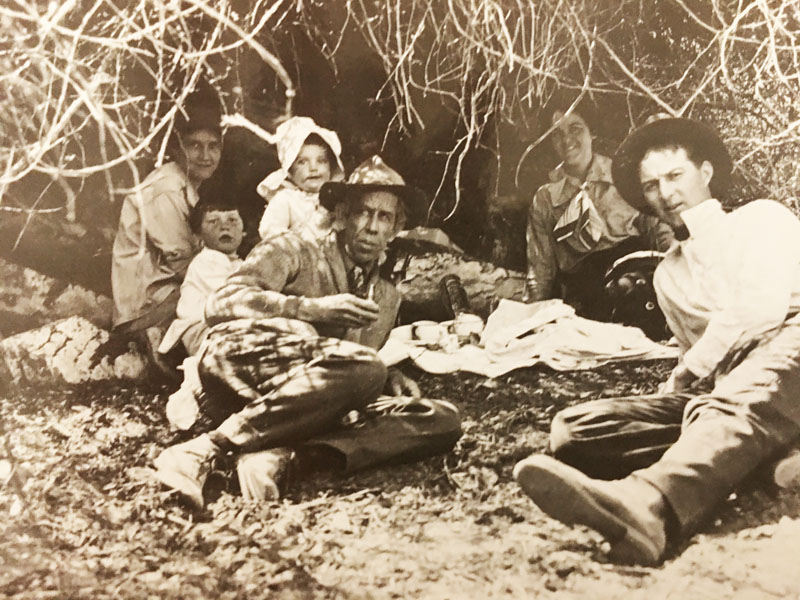
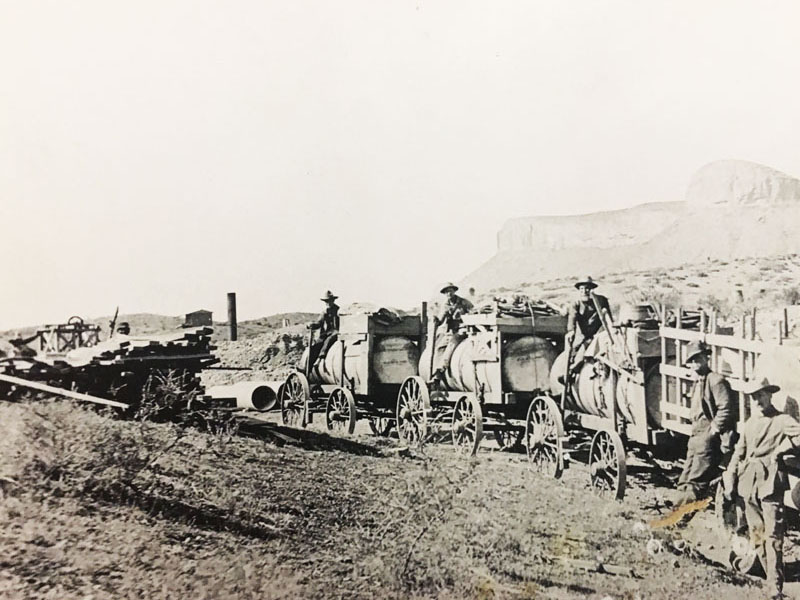
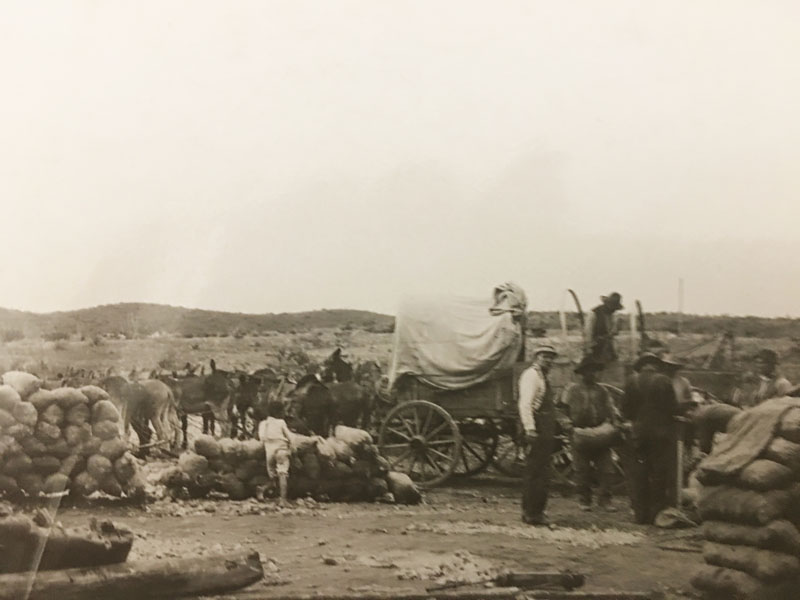
Expedition to Mexico - 1920s
The expedition to Mexico to install several units at a mine occurred in the early 1920's. Some horse drawn wagons and a truck driven caravan carried equipment, wives and children across the plains of Texas to Mexico. Part vacation, part machine delivery, part installation supervision - it must have been a real adventure!
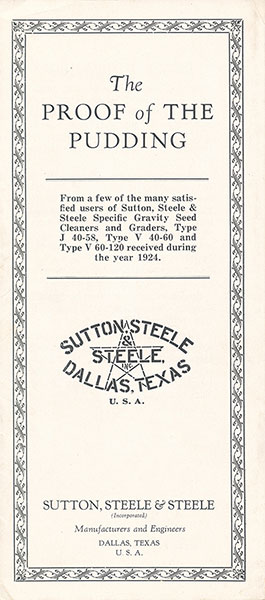
Proof of the Pudding, 1920s - Download Brochure
Plants around the world were processing a diverse range of bulk materials: seeds, peanuts, peas, beans and corn; industrial minerals including beach sands, coal and some metallic mineral ores; cork, chemicals and many others. A brochure produced in 1924 detailed customer letters about the use of SSS equipment.
In 1929, Walter Steele dies in November at the age of 63. Edwin is elected President of the company.
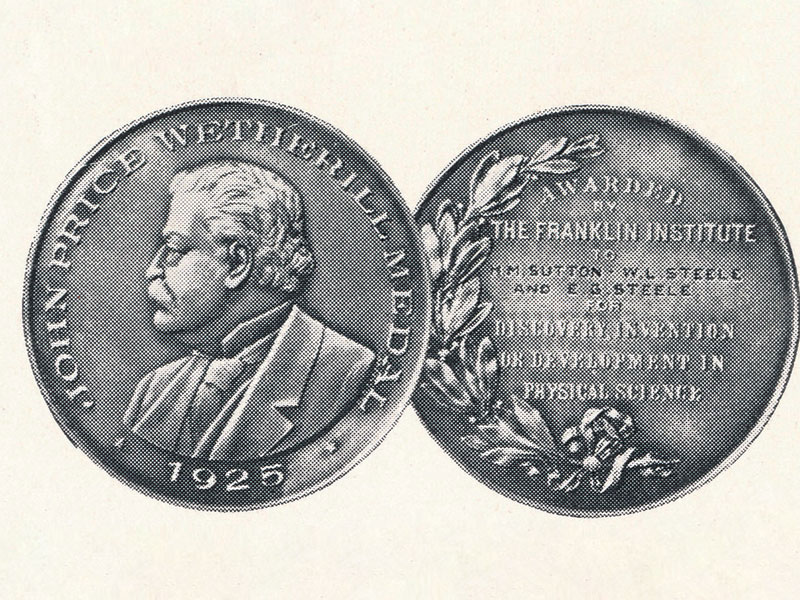
John Price Wetherill Medal of 'Discovery, Invention or Development in the Physical Sciences'
In 1931, The Franklin Institute of Philadelphia awards Sutton, Steele & Steele the John Price Wetherill medal of “Discover, Invention or Development in the Physical Sciences”. The next decade would see great change in the company.
In 1934, Overstrom & Sons was established in Alhambra, California. They designed and manufactured the first vibrating screens for de-sanding rotary drilling mud, along with other kinds of screening and conveying equipment.
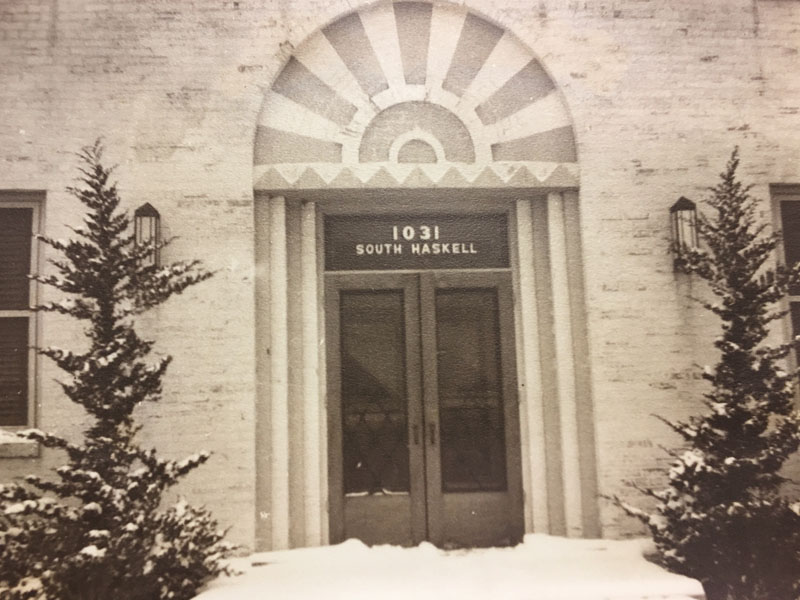
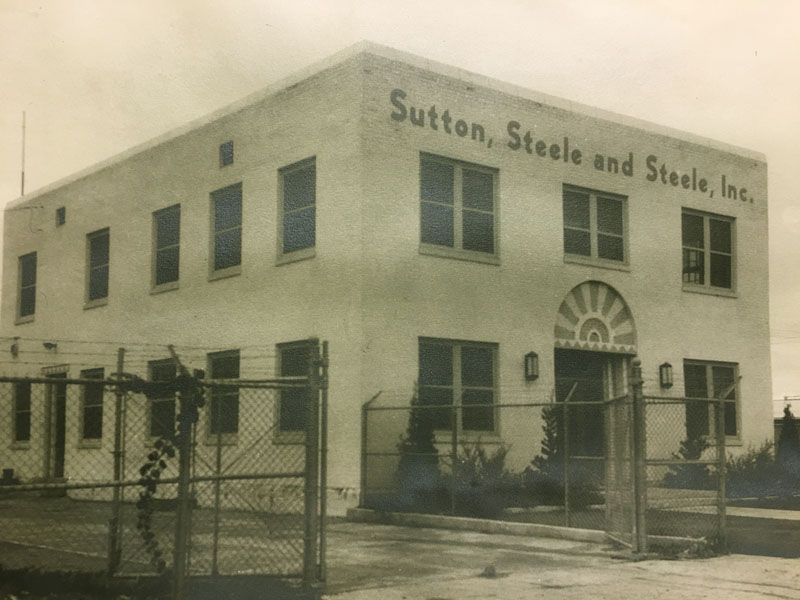
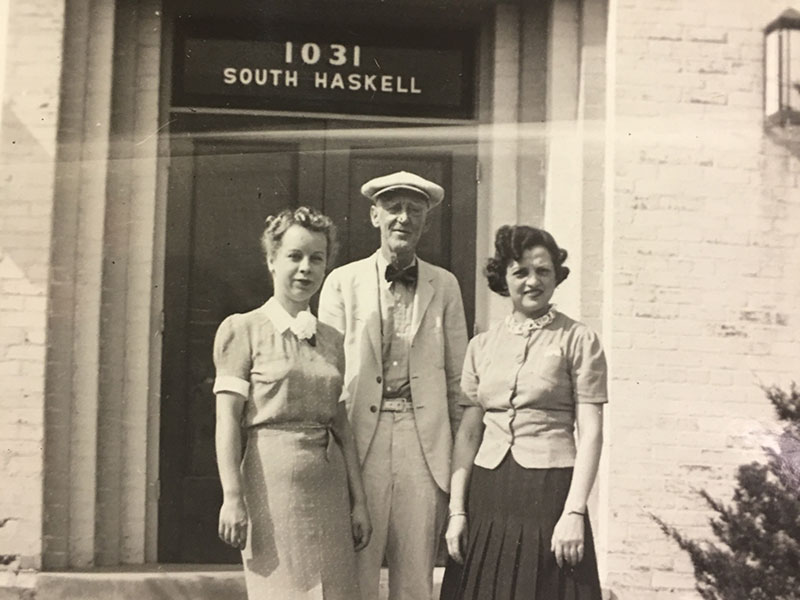
1936 Office and Engineering Building
A new office and engineering building was completed in 1936, facing Haskell Avenue.
The new Art Deco building was completed in the same year of the Centennial Texas State Fair. Archives show Sutton Steele & Steele built the ticket boxes for the fair that year as well.
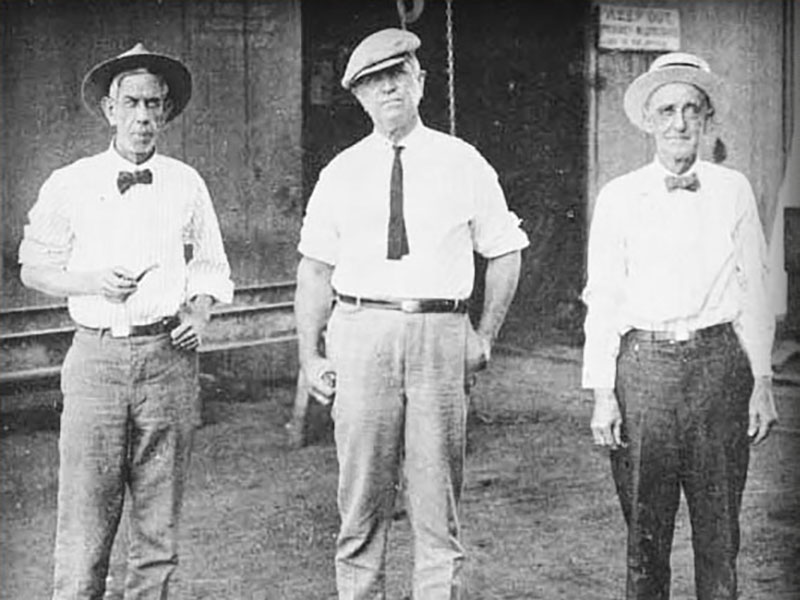
The Big Three. The last photo of the original founders in the archive of the company.
In 1938, Edwin Steele dies at the age of 64. Henry becomes President of the company. Four years later, Henry dies at the age of 79. The three founders are all gone. The widows of the founders assume the ownership of the company.
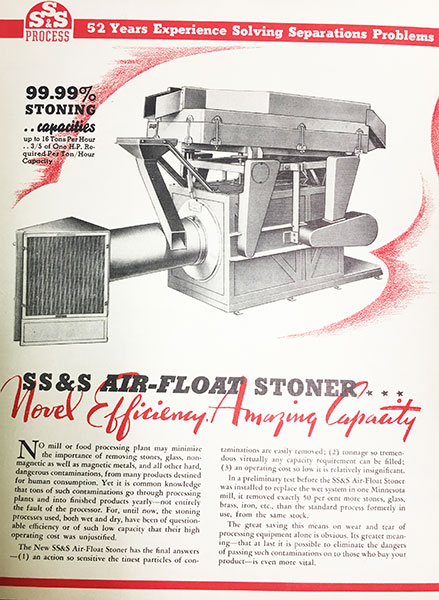
1940s Advertisement
The company advertised in many publications throughout the 1940's.
During World War II, the first efforts to chop scrap wire and cable were done to recover the rubber insulation – not the aluminum or copper. Sutton Steele & Steele supplied a granulator to General Cable for a wire processing facility in Rome, NY. Little did they know what business that first granulator would lead to 20 years later.
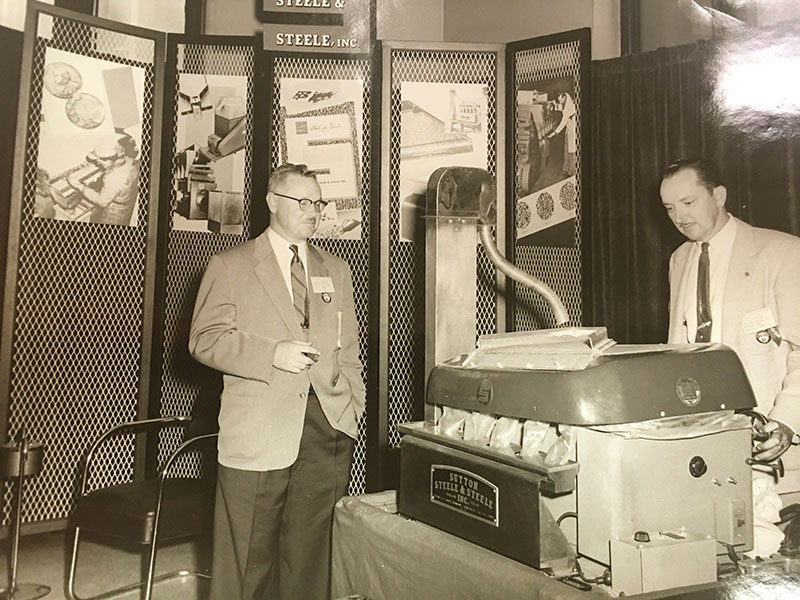
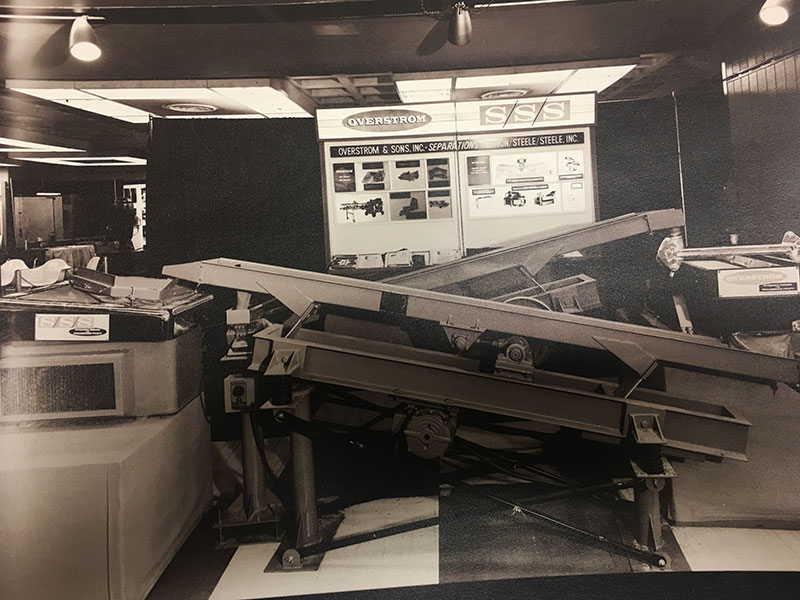
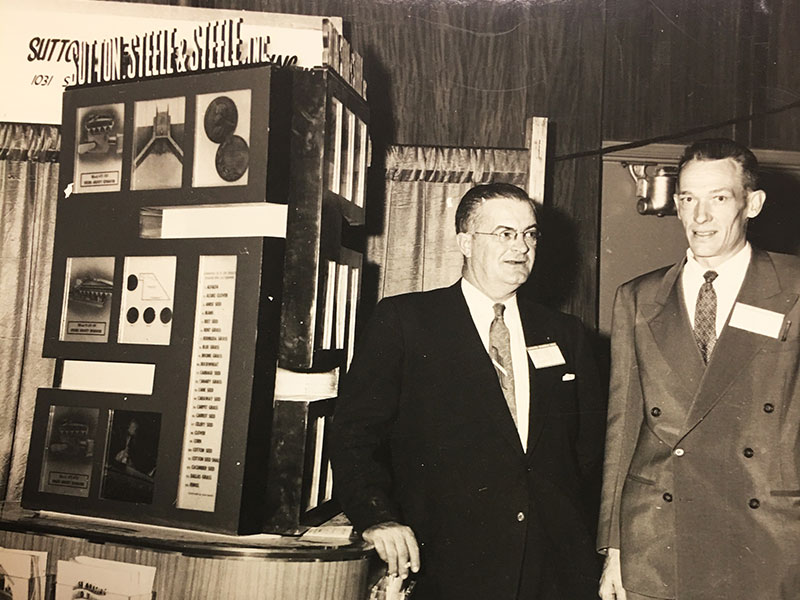
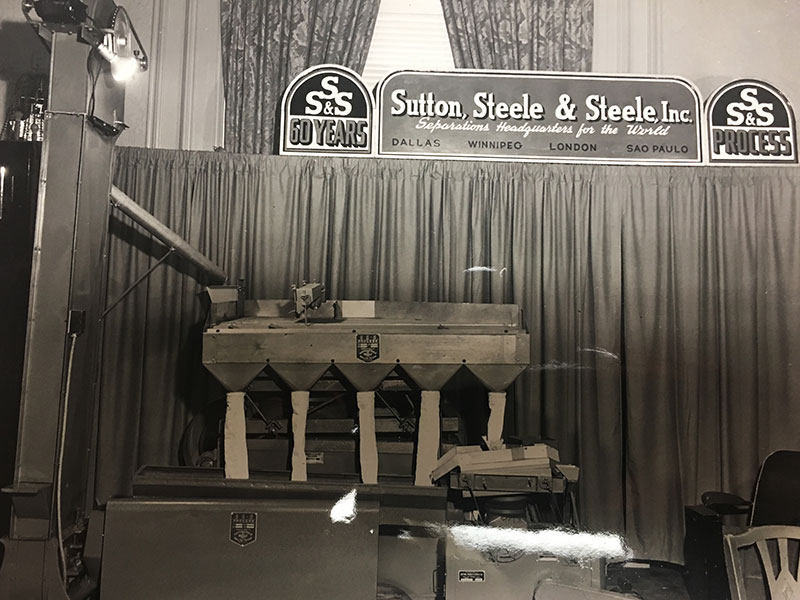
Tradeshows in the 1940s and 1950s
We have a long history of trade show attendance. This image gallery showcases those early years.
In 1954, a young engineer from Minnesota, James F. Sullivan, is hired to work in the laboratory and quickly developed a small gravity separator, the D-135, a variant of which is still made today.
Sometime in the 1950’s, a partnership was formed between Sutton, Steele and Steele and Overstrom & Sons. These two companies had been eyeing each other for years as complementary to each other.
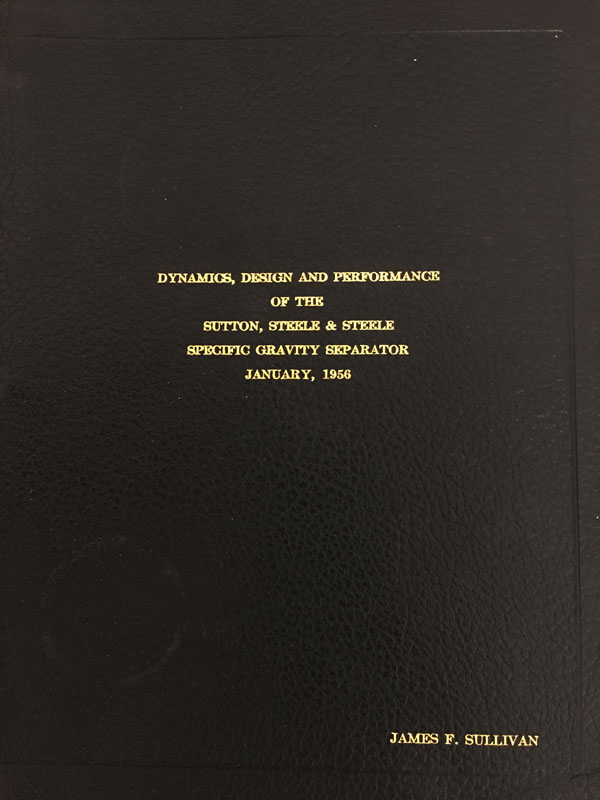
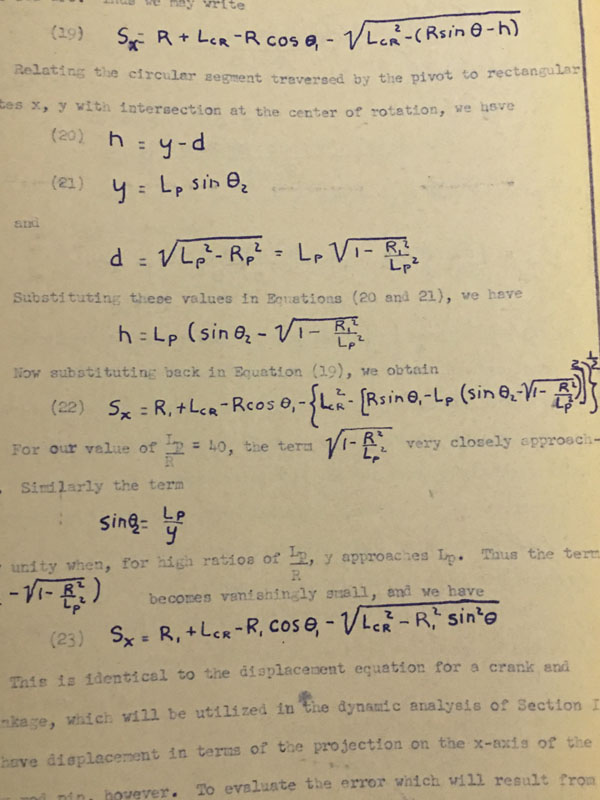
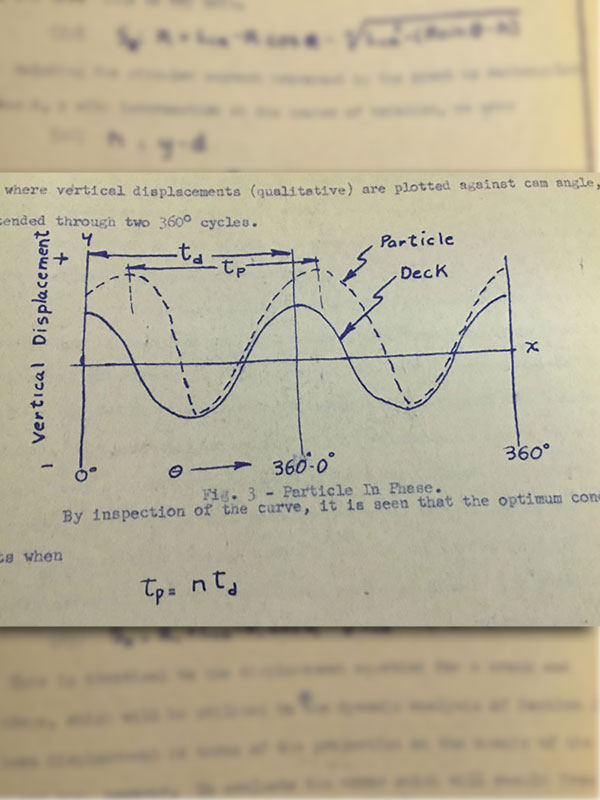
This incredible memiographed 210-page book full of hand written formulas and charts is now being preserved and we will publish a PDF version of it later this year. Look for it on our website.
Sullivan writes the definitive work "Dynamics, Design and Performance of the Sutton Steele & Steele Specific Gravity Separators January 1956”.
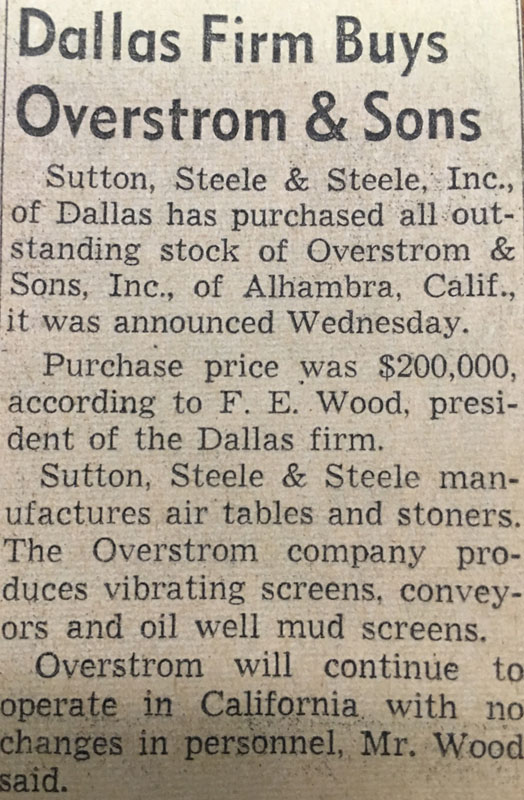
1959 Dallas Newspaper Article on Overstrom & Sons Acquisition
Finally, in 1959, two long parallel lines, marked by hundreds of patents, finally came together when Sutton, Steele & Steele acquired Overstrom & Sons.
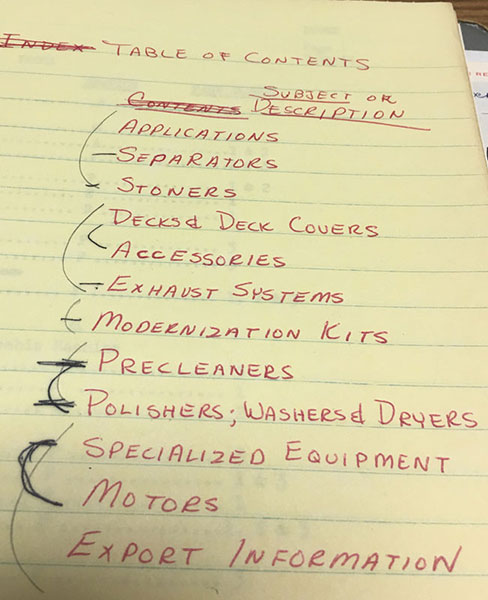
Handwritten Product List from 1966
In 1963, Frank E. Wood, longtime President of the company, dies. The widows of the founding partners promote Sullivan to manage the company as President.
A handwritten index from 1966 shows separators and stoners still dominated the product list. But that was about to change.
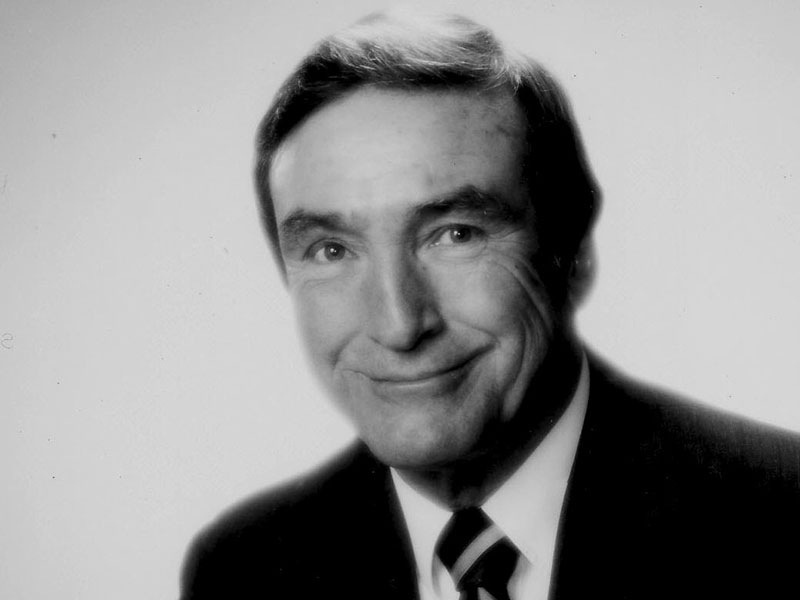
Photograph of James F. Sullivan - 1970s.
The widows agree to sell the company to Jim Sullivan in 1968. He quickly combines Overstrom & Sons and Sutton Steele & Steele. The corporate name is changed to mark the new ownership and honor the founding fathers. The Triple/S Dynamics era begins.
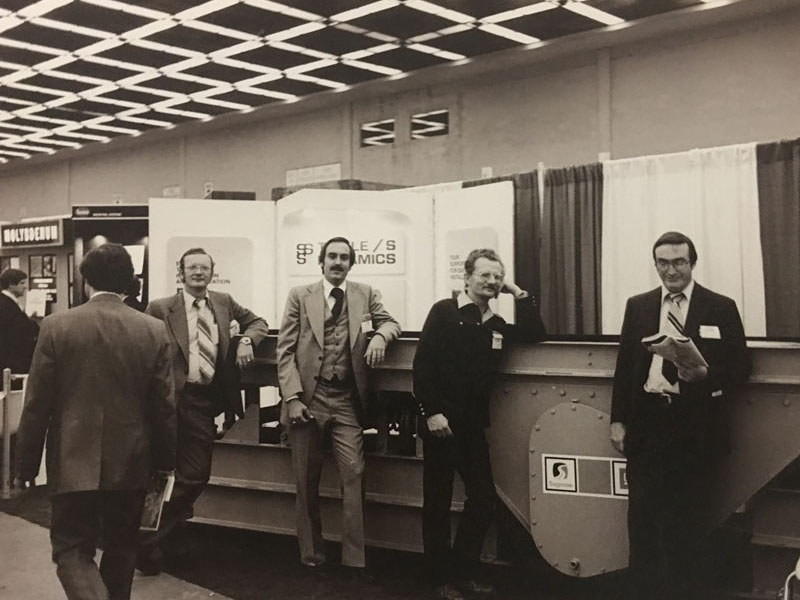
James F. Sullivan and others at Tradeshow - 1970s
The 1970’s brought change and a youth movement to T/SD, along with bell-bottom jeans, tie-die t-shirts, and really wide ties.
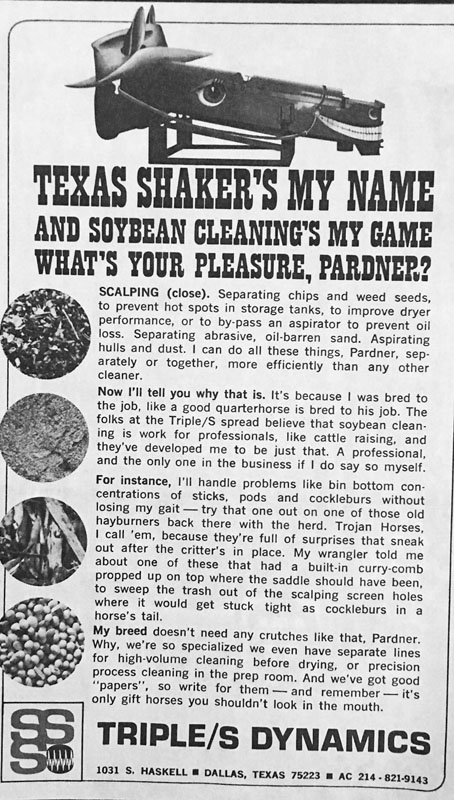
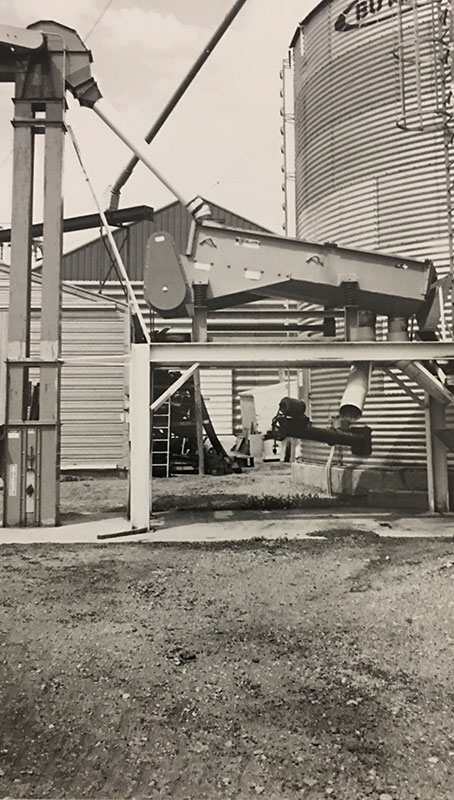
The Texas Shaker vibrating screen took the grain industry by storm in the 70’s. Between 1973 and 1980, over six hundred “standard” Texas Shakers were sold. It also brought with it some really bad advertising, or maybe not.
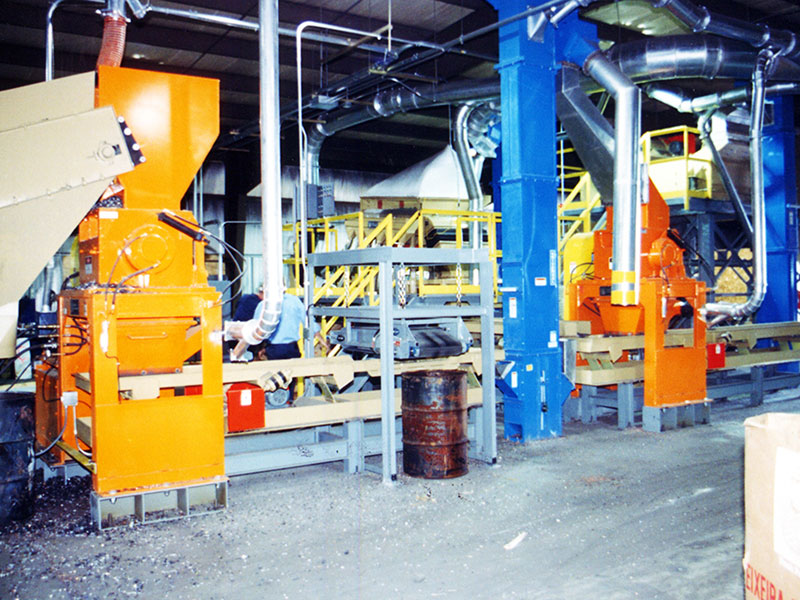
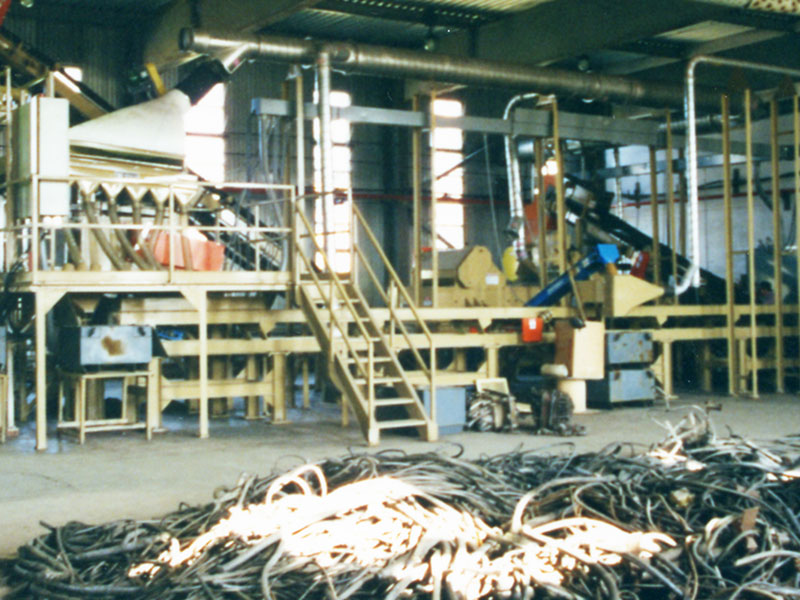
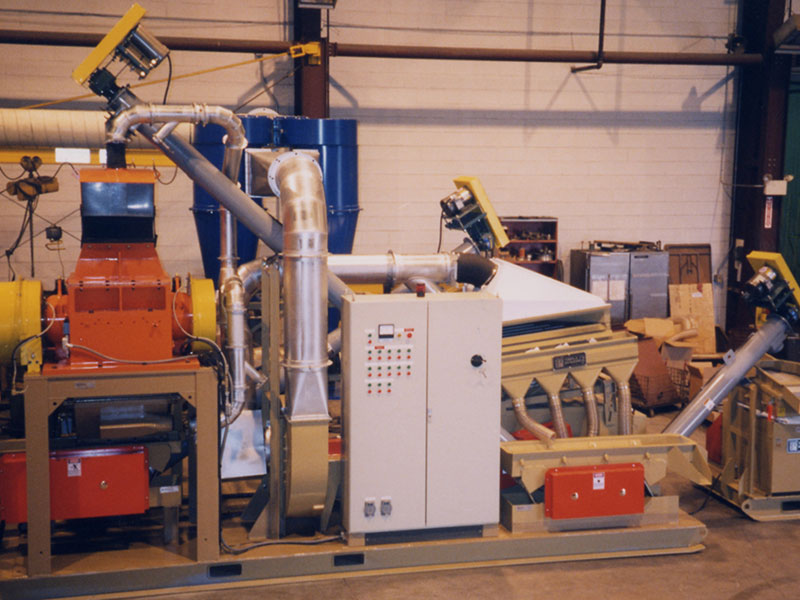
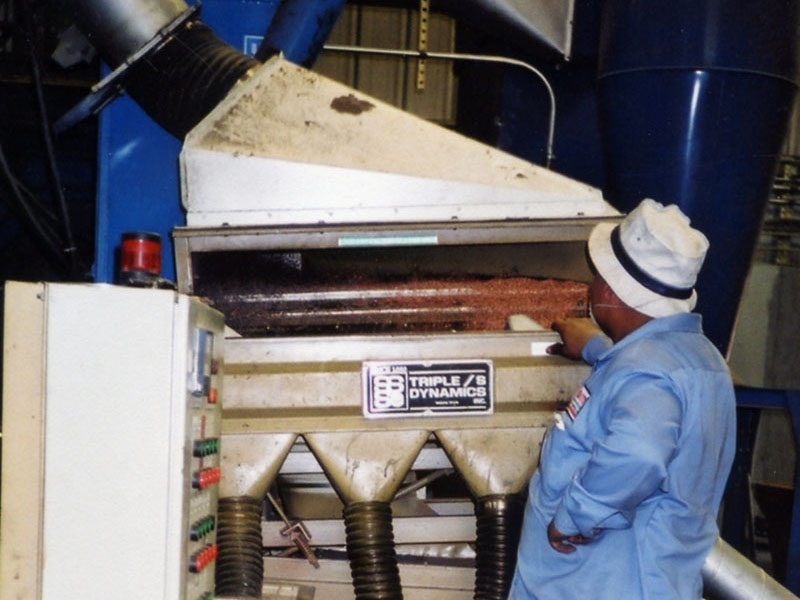
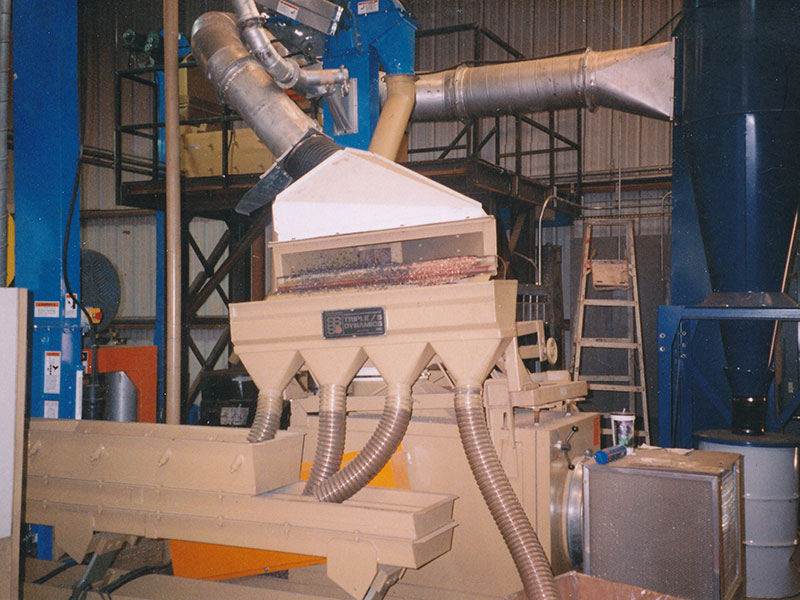
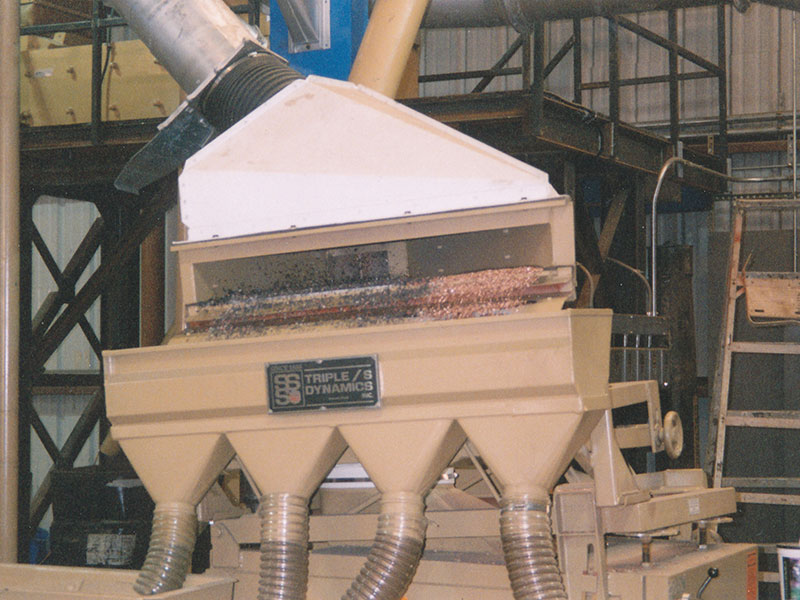
Processing Wire & Cable - 1970s
T/SD engineered the very first system for the recovery of metals from scrap wire and cable in the 70’s, many still in operation today. Between 1970 and 1980 over 150 granulators were sold in systems to recover copper. Almost all of the systems built today by other companies are modeled after the T/SD layout.
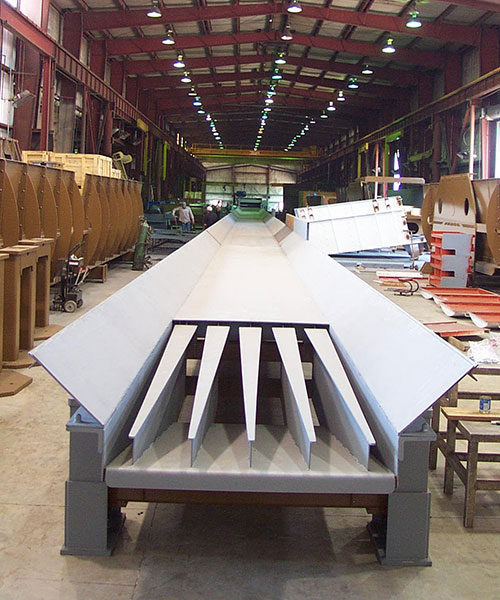
WTE Slipstick in Manufacture - 1980s
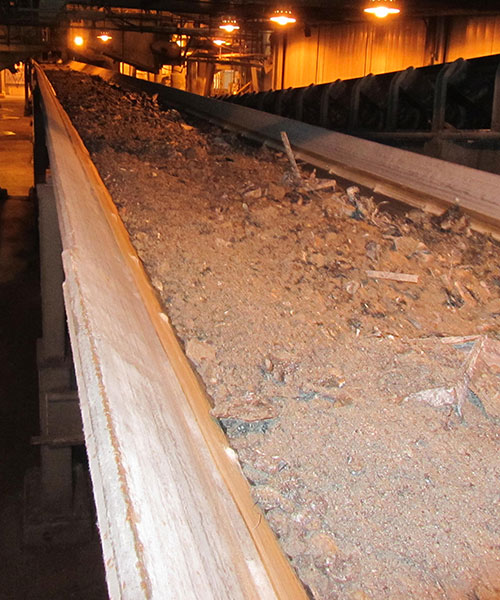
WTE Slipstick Installed - 1980s
In the decade of the 80’s, T/SD built some really big Slipsticks manufactured for foundries and waste-to-energy companies. These conveyors were some of the largest T/SD had built to date, 220 feet long, 12 inches deep and 4 feet wide. This decade also saw the first Slipsticks sold into the food processing industry.
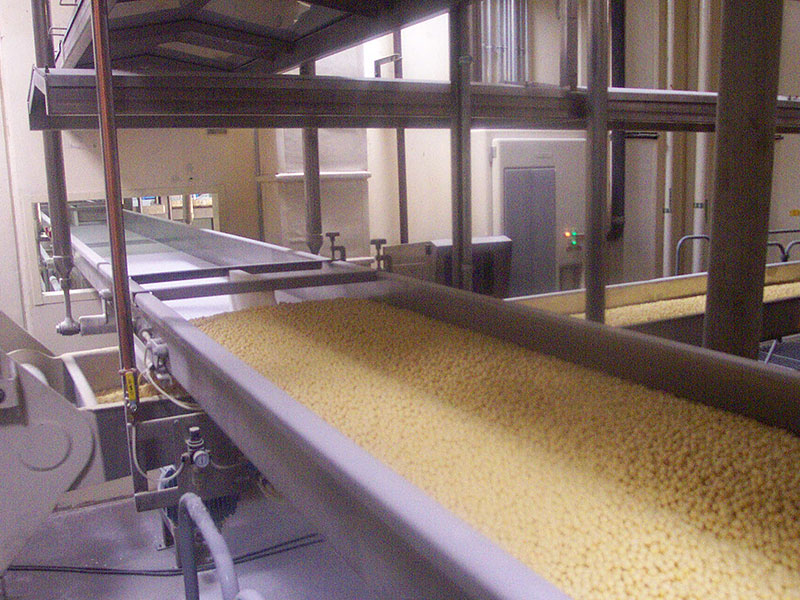
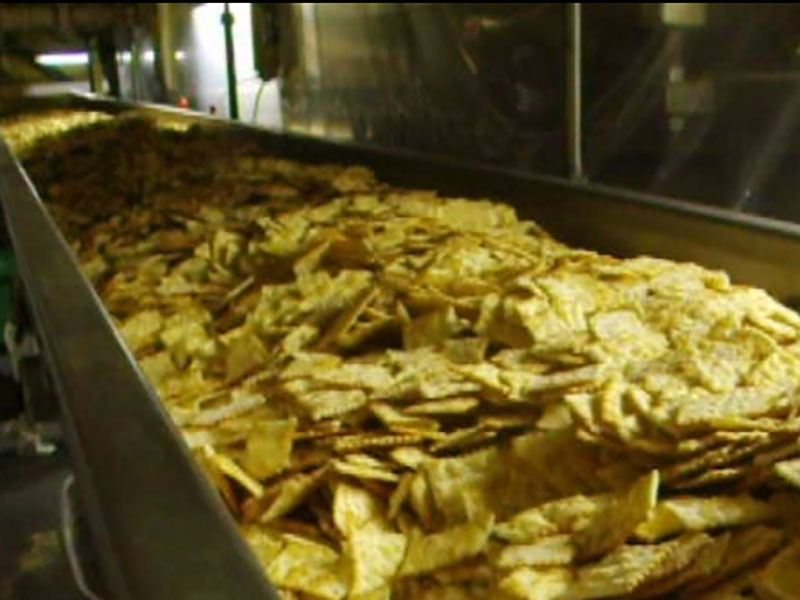
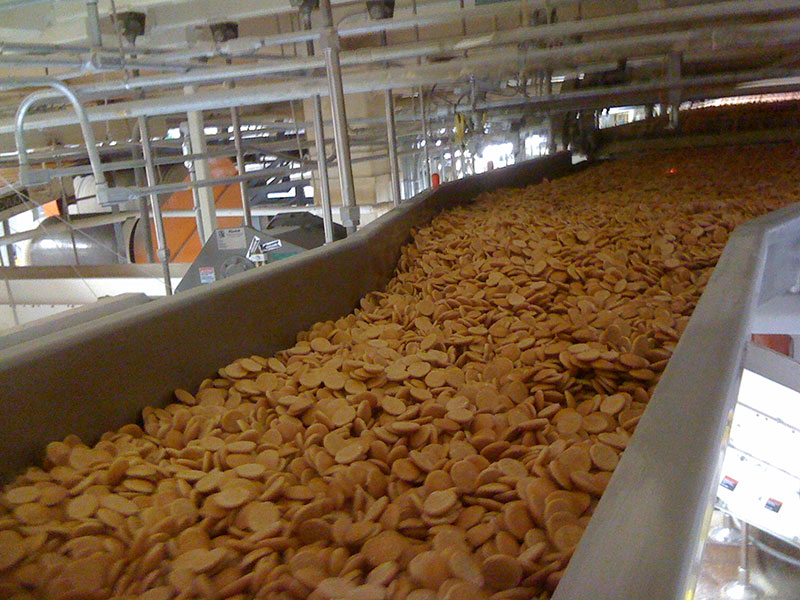
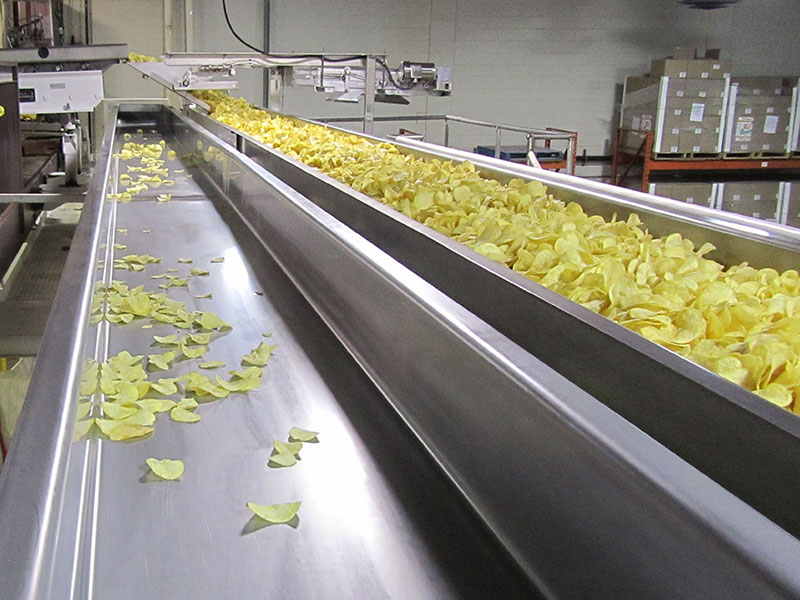
A cereal manufacturer installed a test unit in their lab. T/SD engineers were there to run it and witness the test. The future customer said, “It doesn't break our flakes”. The T/SD engineer asked if that was important. The future customer replied, “It is our number one complaint”. To say it was watershed moment for both the customer and T/SD is an understatement.
Some of the first food manufacturers to try this new type of conveying method were cereal companies. They bought Slipsticks because of the gentle handling characteristics of horizontal motion conveying. What started with cereal, quickly exploded across the entire food industry – cereal, chips, snacks, meats, beans, vegetables, coffee, almonds and candy. The Slipstick became the biggest product in the T/SD portfolio and still is today.
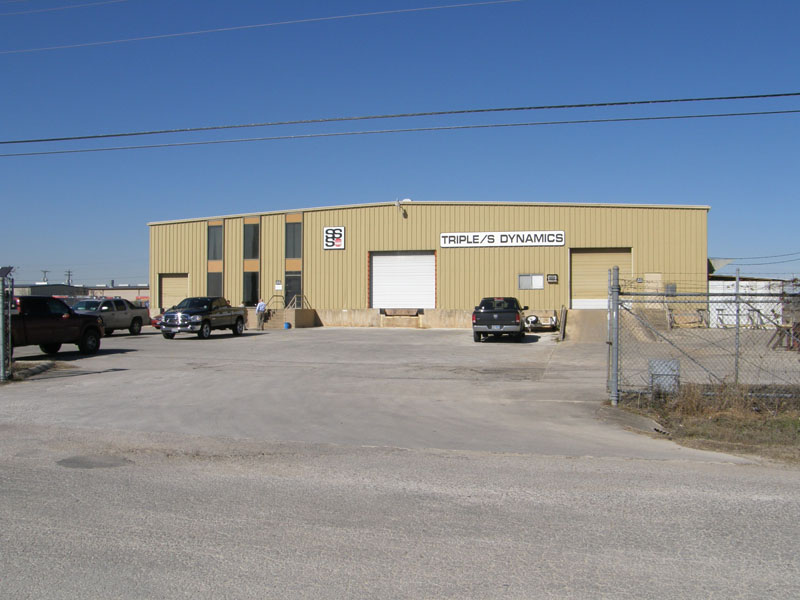
New Manufacturing Facility in Cibolo, Texas - 1984
T/SD took a bold step in 1984 opening its third manufacturing facility in Texas, this one in Cibolo, a suburb of San Antonio. Jay Sullivan moved south to become the Plant Manager. This facility was earmarked to be the stainless steel location – a new home for the Food Slipsticks.
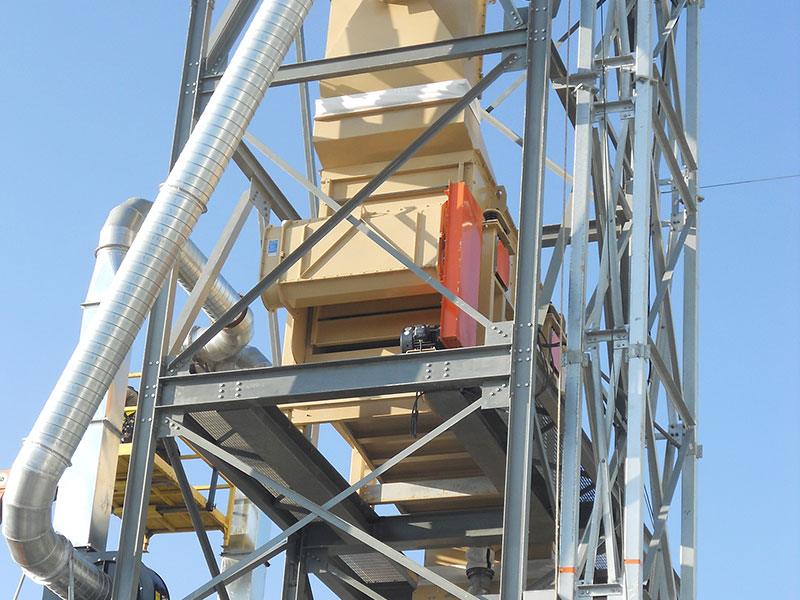
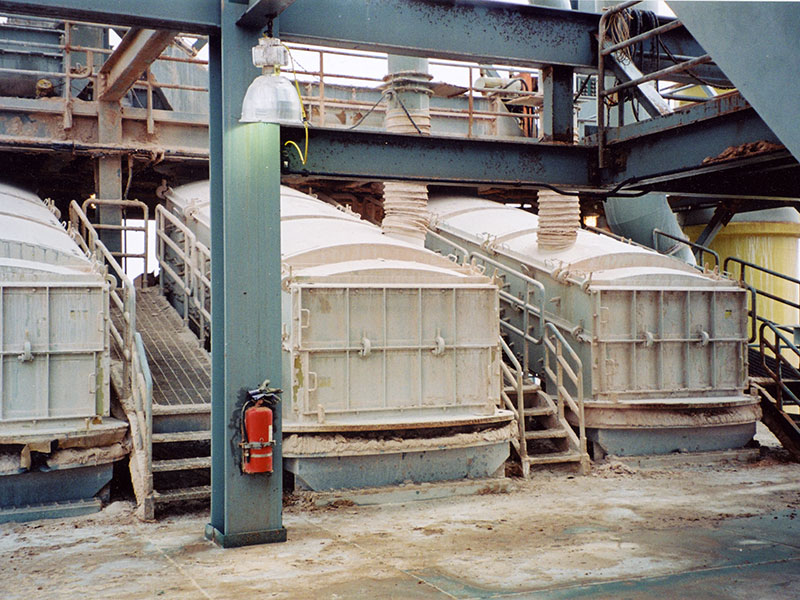
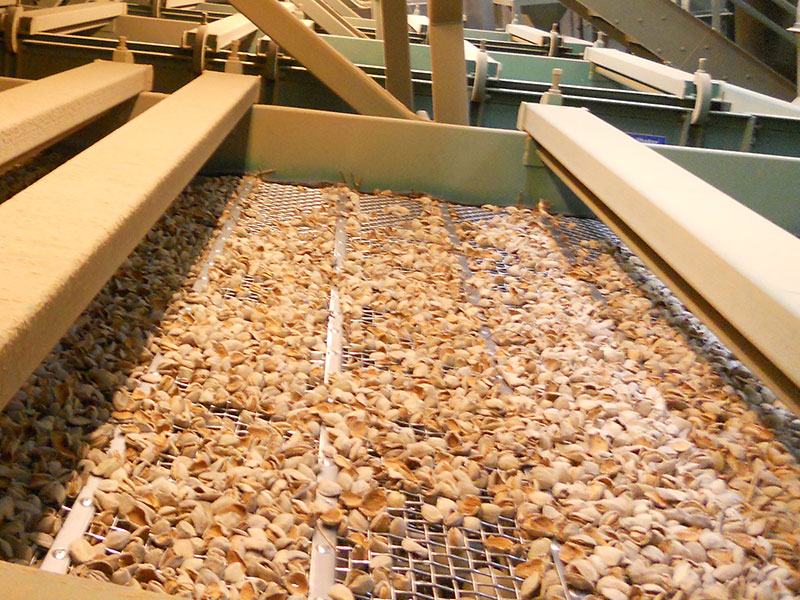
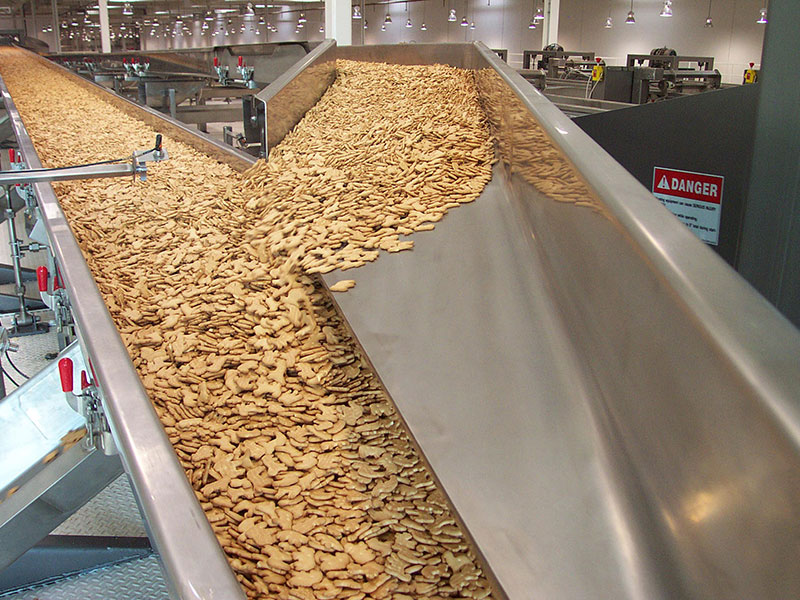
The decade of the 1990’s turned out to be one of the biggest in the company’s history. New applications for the Texas Shaker and the Slipstick.
Both manufacturing locations were full – building record numbers of conveyors, screens and separators. But there was much more to come.
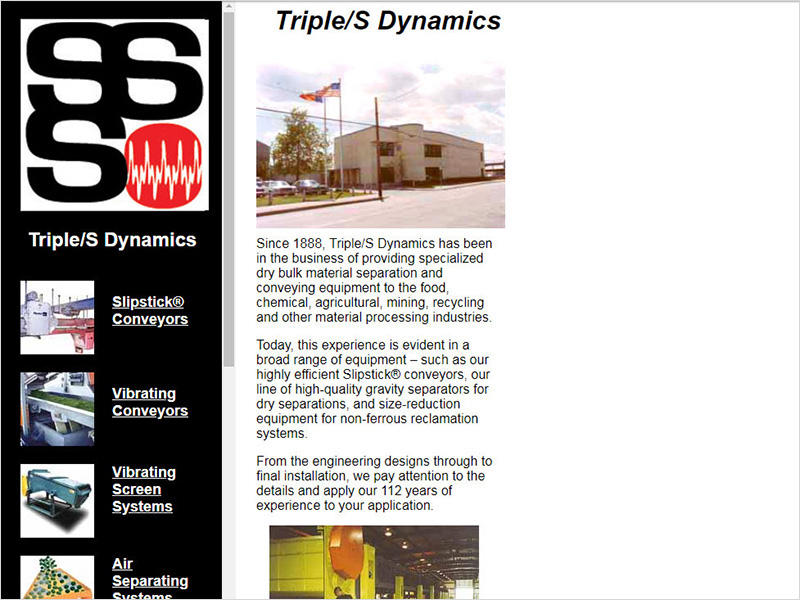
2000
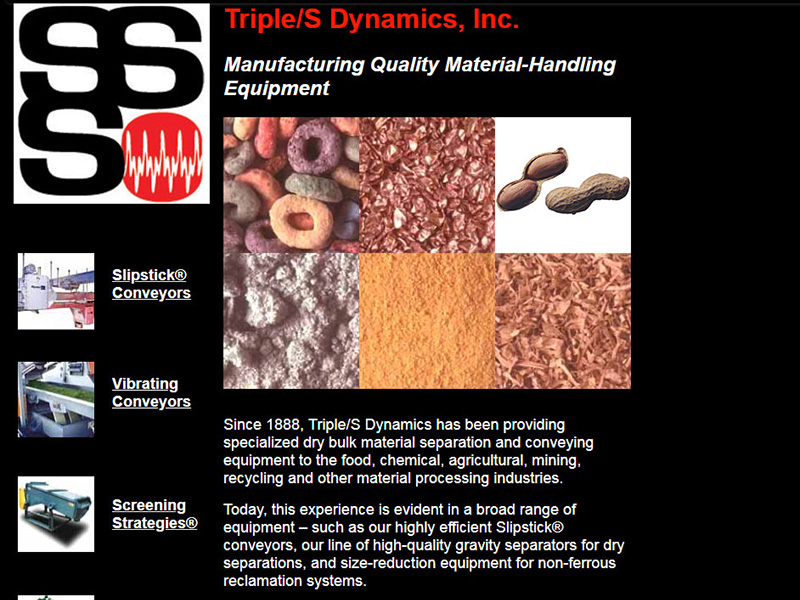
2001
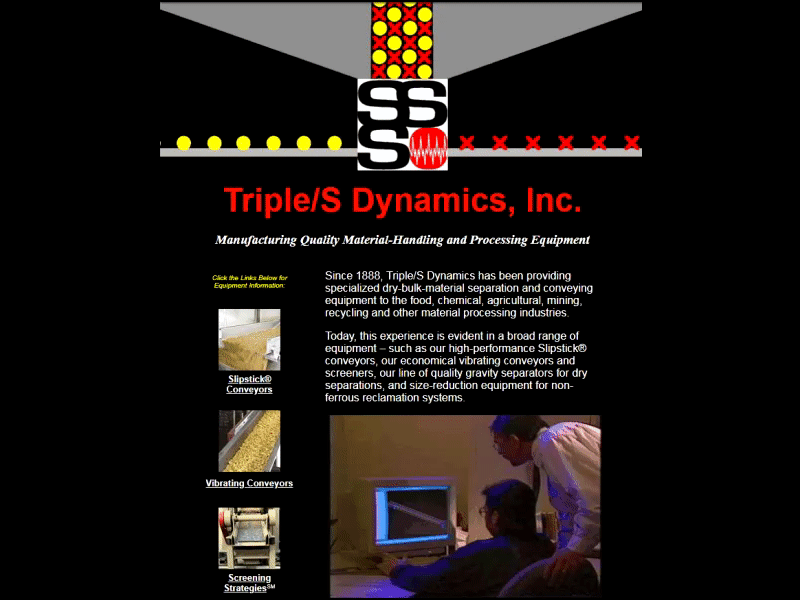
2004
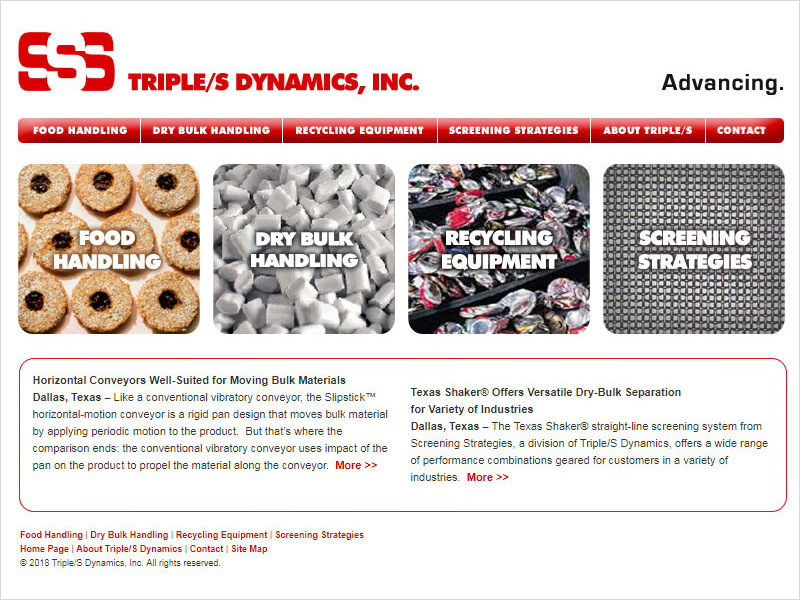
2006
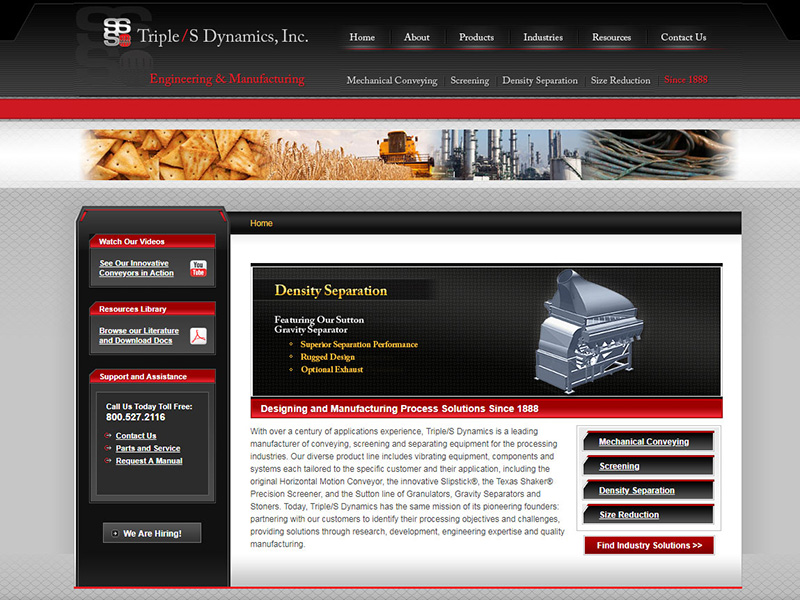
2012
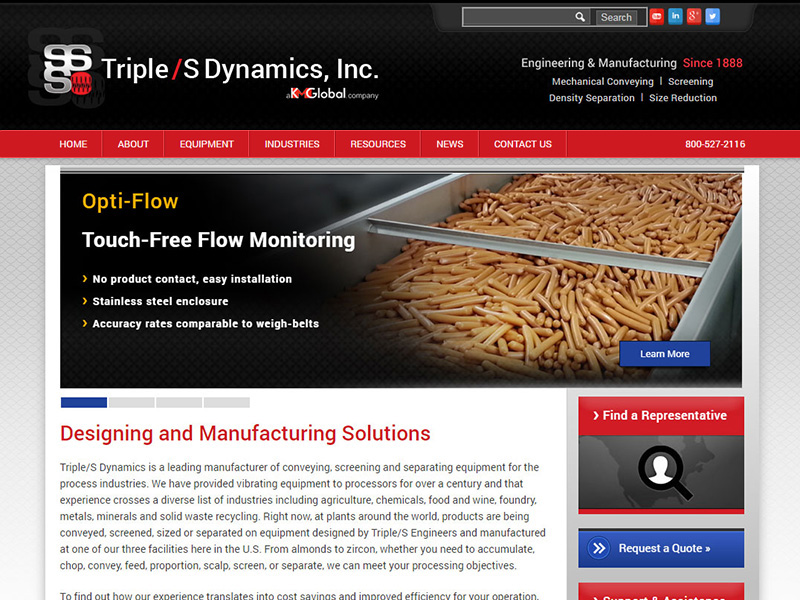
2014

2016
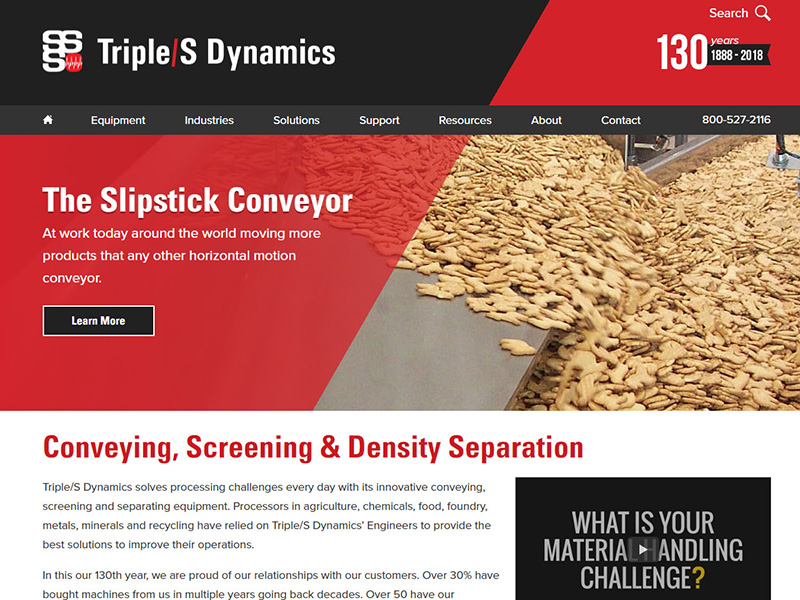
2018
Evolution of Triple/S Dynamics Websites, 1998-2018
T/SD’s first website was launched in 1998, only a few pages deep, it was updated in 2000, 2001, 2004, 2006, complete redo in 2012, a redesign in 2016 and to the new responsive site that we rolled out in February of 2018.
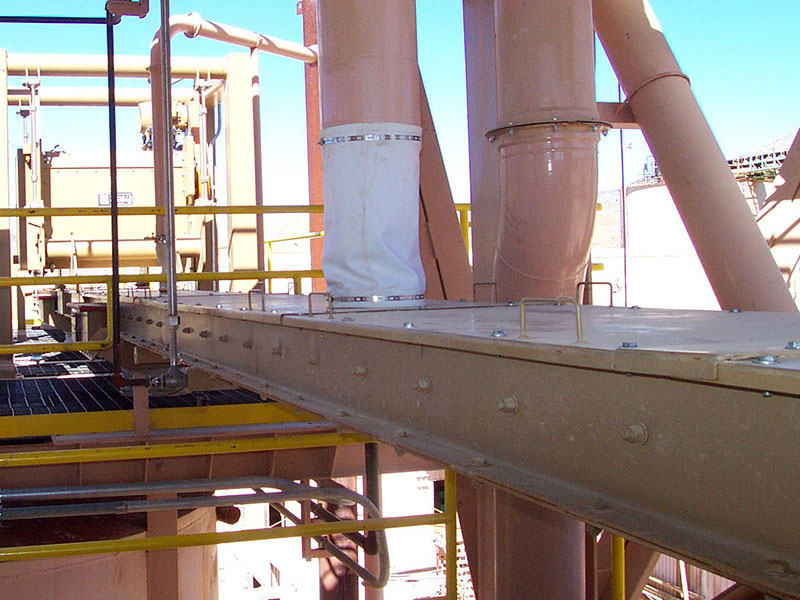
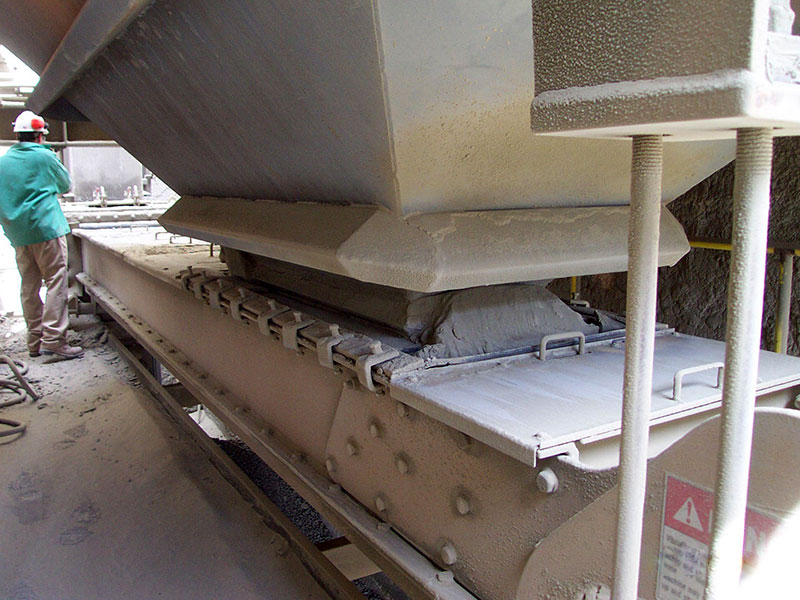
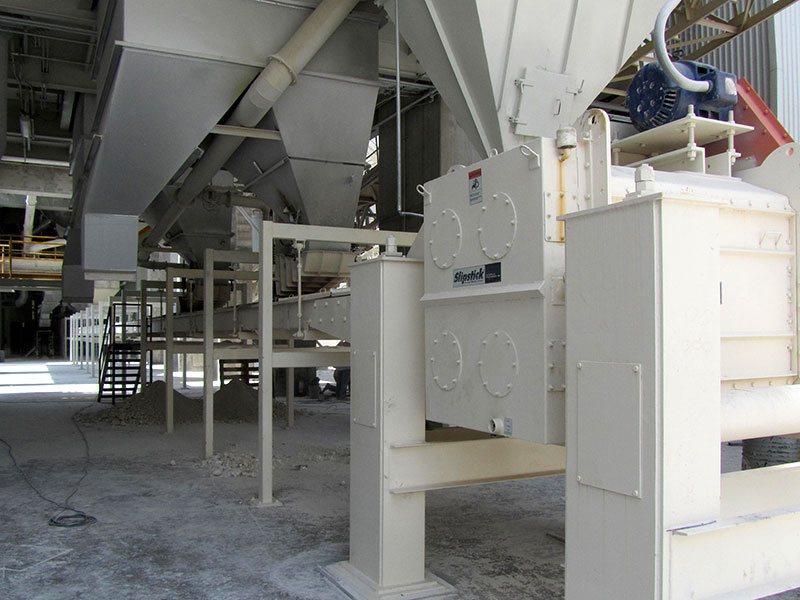
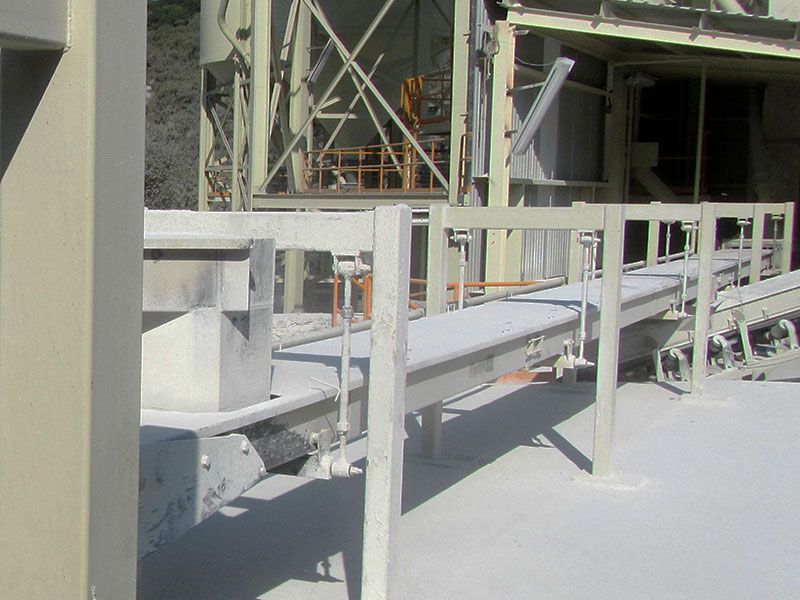
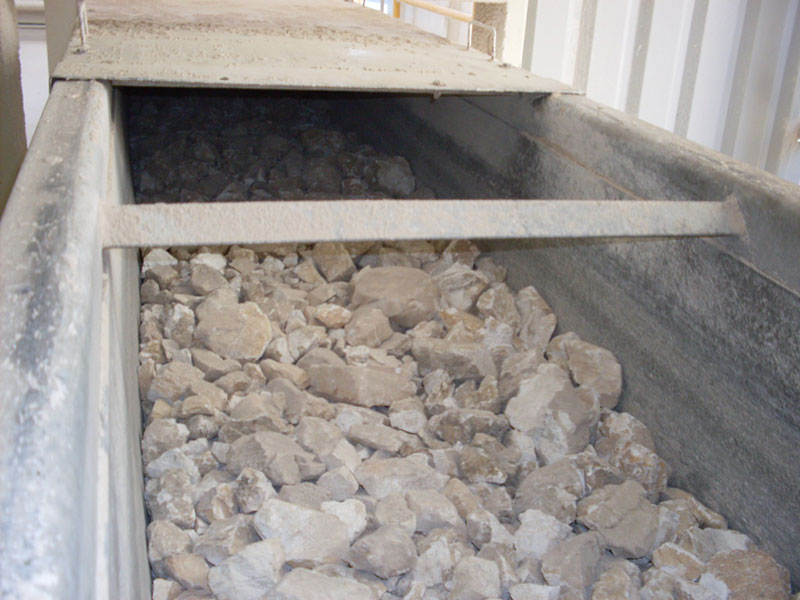
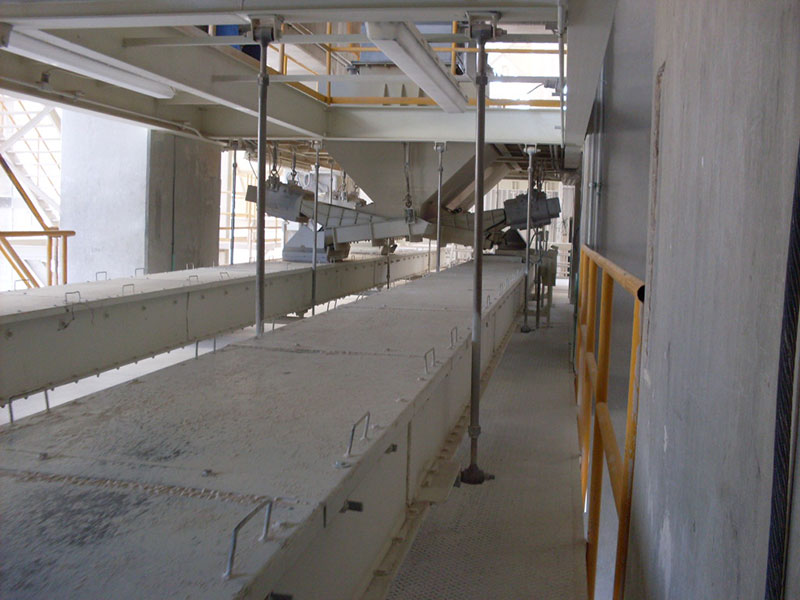
By the turn of the new century, Slipstick conveyors are in plants around the world and in all kinds of markets. While the food business took off, the industrial markets were opening to new applications including: Ash, Activated Carbon, Barium Sulfate, Calcium Carbonate, Calcium Oxide, Carbide, Carbon Black, Cat Iron, Catalyst, Cement Clinker, Ceramics, Detergents, Dextrose, Fertilizers and Weedkillers, Granite, Hydrocarbon Resin, Paper, Potash, Quicklime, Resin, Phenolics, and Plastic Pellets.
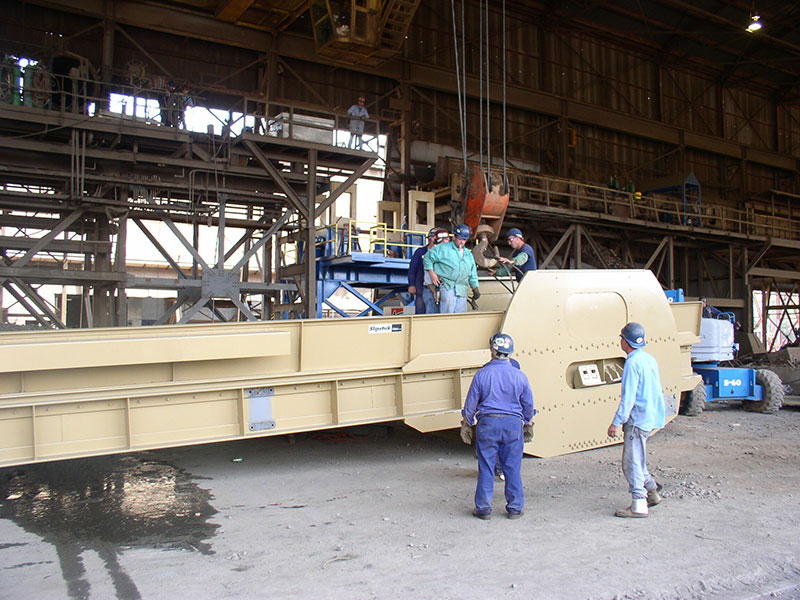
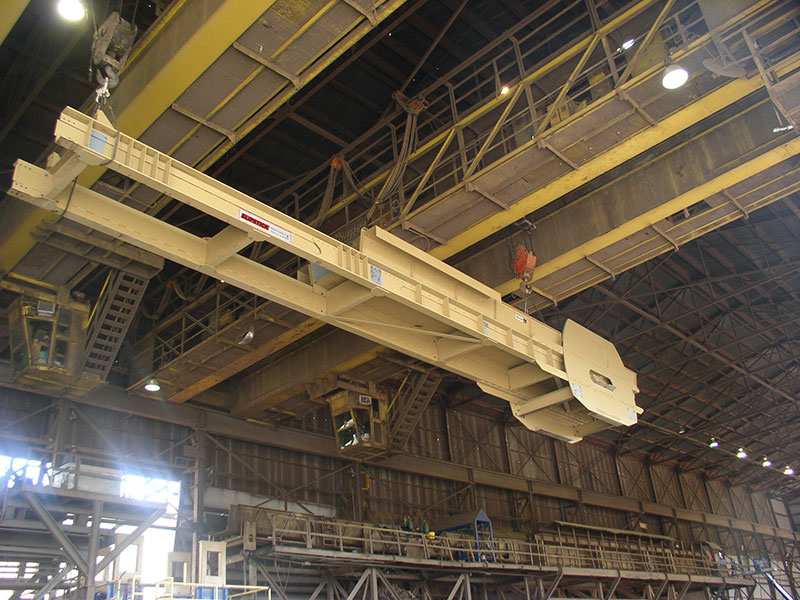
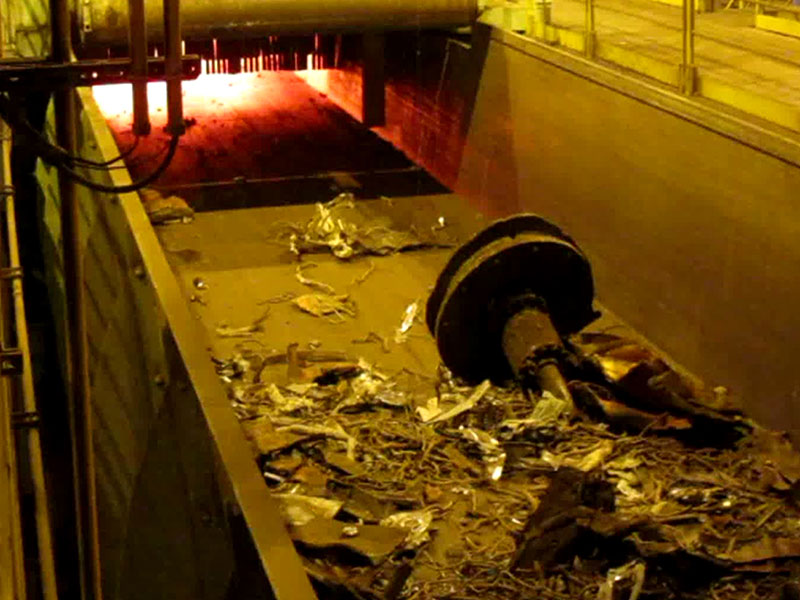
Consteel Slipstick Conveyor
Another chance meeting at a tradeshow became a partnership that led us into the steel making industry. Slipsticks were the perfect choice to feed electric arc furnaces, and we mean some very large Slipsticks – over a hundred feet long, five feet deep and 5 or 6 feet wide, moving 600,000 pounds of scrap steel. Most of those units are still in operation today.

Jeff and Jim Sullivan - 2013
"Renowned for its flagship products, the Texas Shaker grain cleaner and Slipstick horizontal motion conveyor, Triple/S Dynamics is winding down its 125th anniversary year and winding up the transition to new ownership that promises to build on the traditions of the Sullivan family and the founding trio of the Sutton, Steele, and Steele boys in 1888."
In 2011, the Sullivan family sells its 43-year ownership of Triple/S Dynamics to the Thompson family and T/SD becomes a part of the KMC Global group of companies, with its corporate headquarters in Michigan.
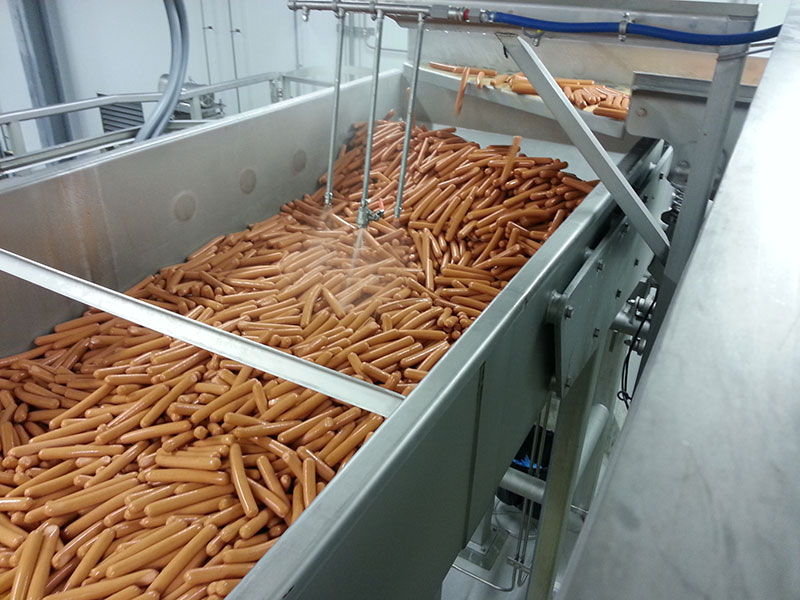
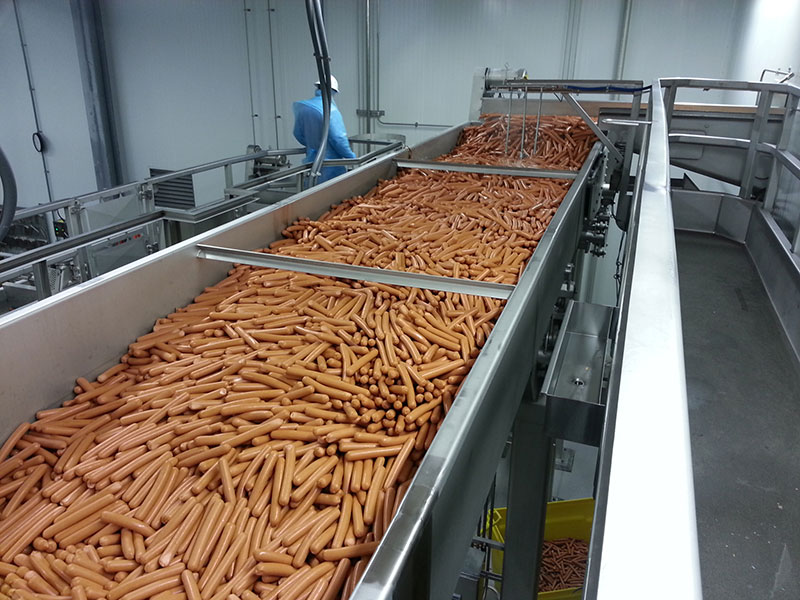
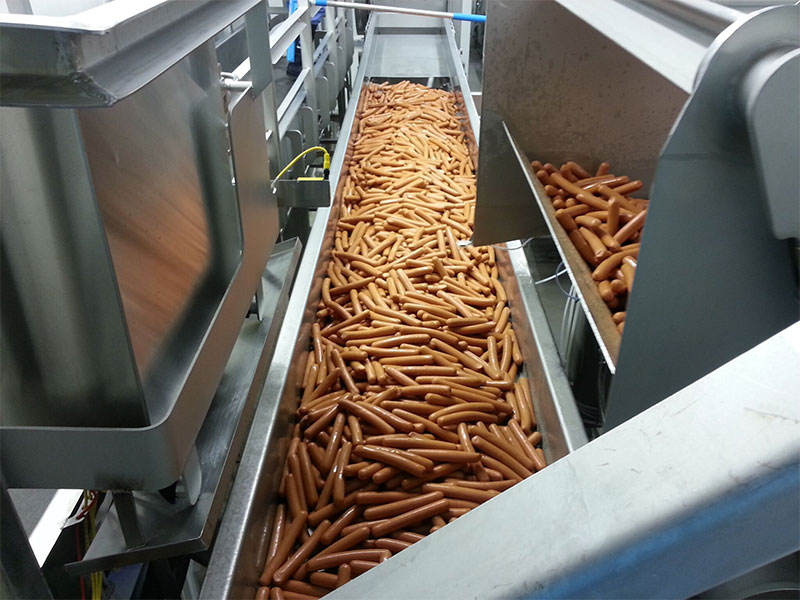
Slipstick In-line Accumulator with Hot Dogs
The Slipstick becomes an in-line accumulator capable of holding over 1000 cubic feet of product without having to move it off-line.
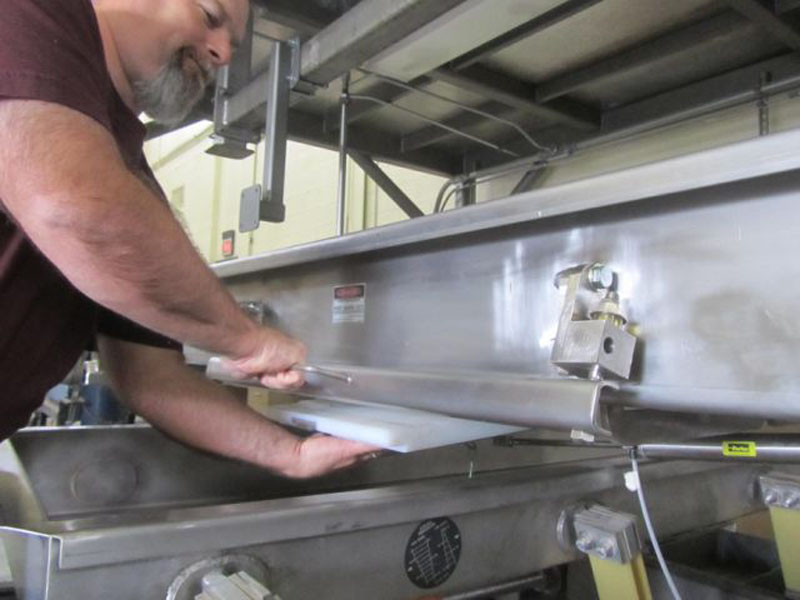
Eco-slide Gate

Vertical Shaft
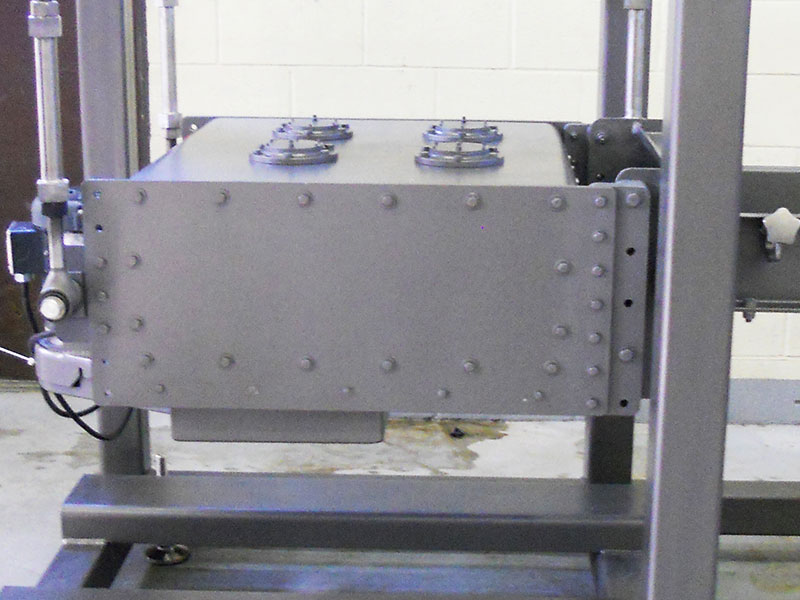
Vertical Shaft
Two major additions to the Slipstick conveyor catalog – the vertical shaft drive and the eco-slide gate. Both quickly become customer favorites.
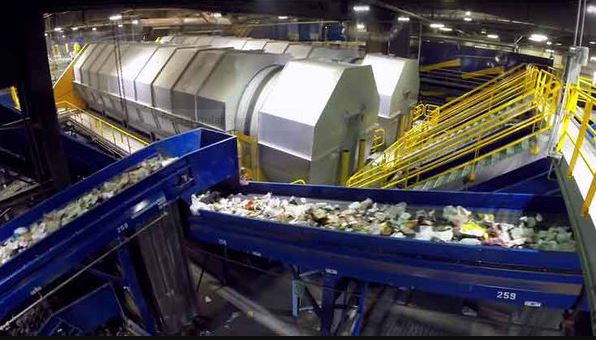
Large Rotascreen Trommels for Solid Waste Processing
In 2014, Triple/S built two of the largest rotary screens (trommels) to date for a solid waste processor in California. The two units both 12’ in diameter and 48’ long are installed screening 65 TPH of solid waste.
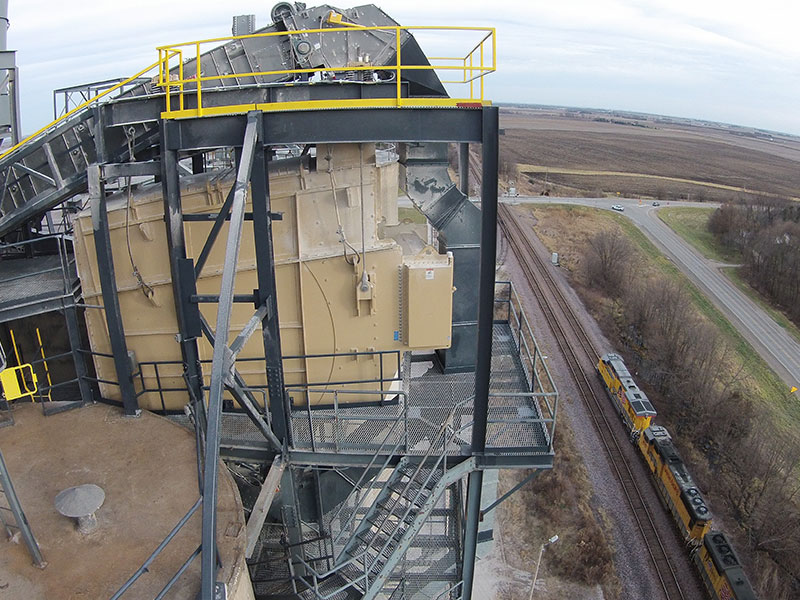
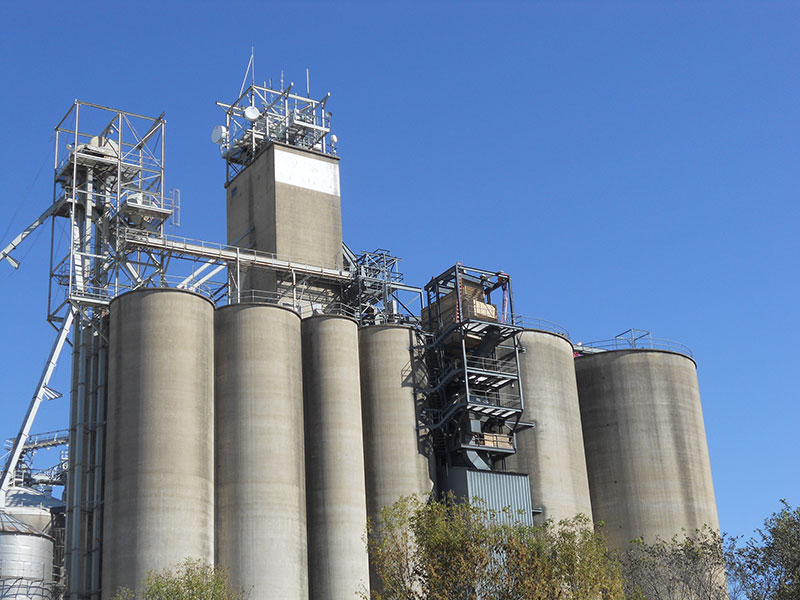

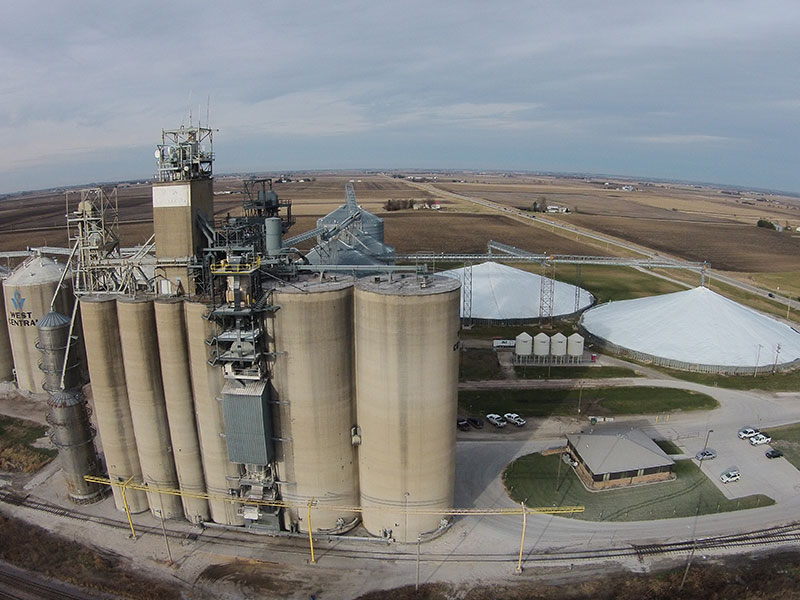
Large Texas Shaker Vibratory Grain Cleaner - 2015
In 2015, Triple/S engineered and manufactured the largest Texas Shaker® vibratory grain cleaner yet, a 55,000-lb. system that scalps corn at 60,000 BPH. 60,000 BPH is 3,000,000 pounds per hour!
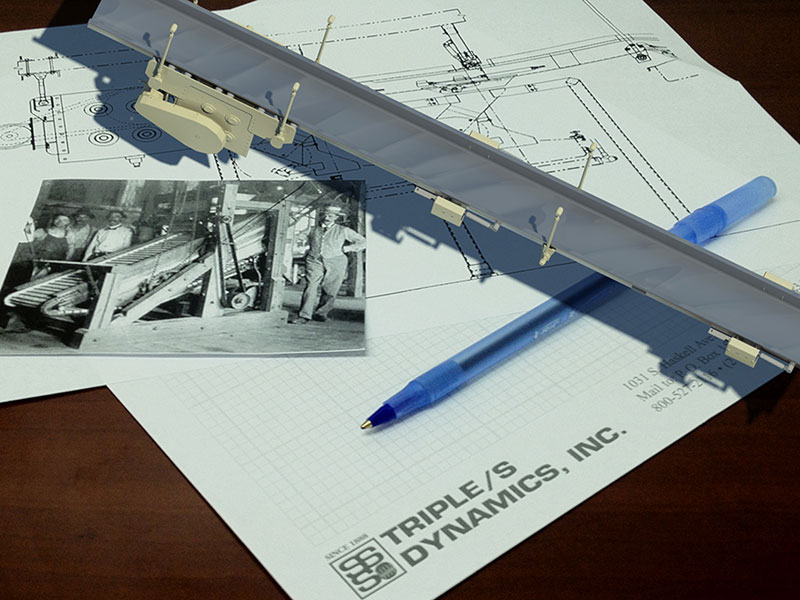
In 2017, a new leadership team was put in place at T/SD. The company is reshaping itself to continue to provide the best solutions for our customers. The spirit of the founders of the organization is the valued heritage of the present. We view our company’s past record of achievements as a means to greater accomplishments in the future, a foundation of experience for new applications, new designs and innovative concepts for the processing industries through research, development, engineering expertise and quality manufacturing.
Ask an Expert
Ask Our Team of Experts
We can help solve your material handling challenges.