All-New Production Line for...
Gravity Separators
Density separation is achieved with basically two components, mechanical vibration and air fluidization.
The Gravity Separator makes a highly sensitive dry separation on the basis of one of three particle characteristics: density, size or shape. When size and shape are controlled within certain limits, the gravity separator is unmatched in its ability to separate a complex mixture by density. The relative size and shape of each component of the mixture also bear on the efficiency of the separation. Wide variations in these material characteristics can dramatically affect the separation results.
Density Separation Equipment Applications
Where a wide range of particle size is present, screening may be required to segregate materials into manageable size ranges prior to separation. Where significant variations in shape are found to be detrimental to separation efficiency, size reduction may be added to the process. These factors become more important as the densities of the material to be separated become closer.
In some cases, test separations are the only practical means for predicting separator performance. Triple/S Dynamics maintains a fully equipped separations lab where screening may also be included with trial separations to best determine what equipment and procedure will optimize both machine and process choices.
Form / Function
Triple/S Dynamics Gravity Separators are equipped with a porous deck, which is inclined and subjected to vibration which causes material in contact with the deck surface to convey up the inclined surface of the deck. Low-pressure air is forced through the deck to fluidize the dry mixture so that the lighter materials are lifted from the deck surface and allowed to float down the inclination of the deck. The final result, presented at the discharge face of the deck, is a continuous, graduated progression from the least to most dense, smallest to largest, and least to most aerodynamic.
Equipped with an integral supply air blower, slide-out deck panel and optional exhaust, these machines offer superior separation performance in a simplified and rugged design.
Figure 1 represents a typical cross-section of the material bed at the discharge face, showing how the separated mixture is cut to produce a clean, light tailing by recycling a middling or boundary fraction. In the ideal two part mixture illustrated, size and shape are perfectly uniform, and the middling is only a random mixing at the interface between the light and heavy fractions. The composition of the middling, in actual practice, is often more complex and calls for retreatment by screening, grinding, or other means before returning to the separator feed.
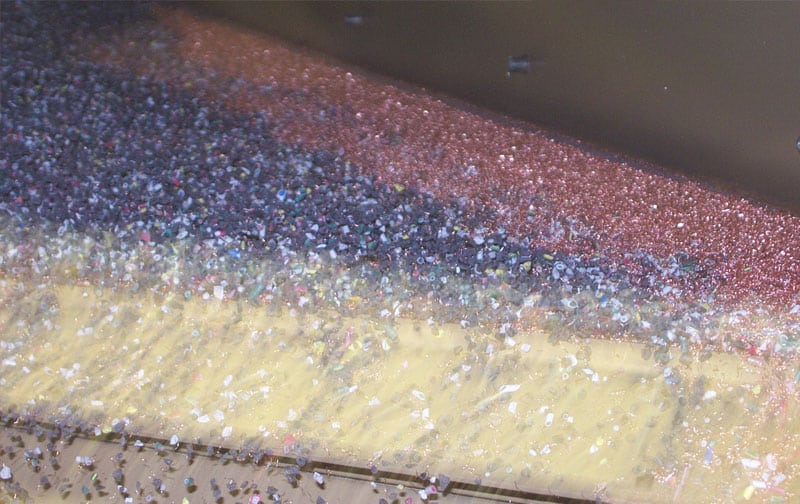
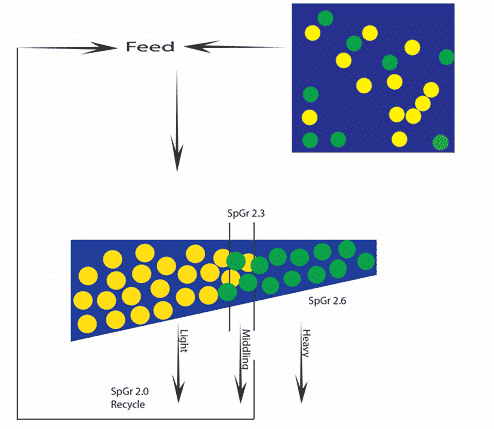
Applications
Any complex dry granular mixture, in a fluidized bed, can be separated into component fractions on the basis of one of three particle characteristics – DENSITY • SHAPE • SIZE, so long as two of these characteristics are controlled within certain limits. Applying this principle, typical separations include:
- Density – quality grading seeds, beans, peas, and corn; removal of stones and glass from peanuts, grain, and other agricultural commodities; metallic prills from crushed slag; copper or aluminum from granulated scrap wire and cable; minerals from gangue; and stones and metal from wood chips, shavings and sawdust.
- Shape – removal of hulls from oilseeds (soybean, sunflower, castor beans, etc.); sticks and stems from leafy spices; shell pieces from nut meats; granules or insoluble from flaked products; mica flakes from gangue; and asbestos fiber from gangue and grit.
- Size – cut points between 35 and 200 mesh, without attrition loss.
Sample test results using a Gravity Separator:
Material – crushed magnesium alloy pot sludge composed of interlocked slag and metallic magnesium sized 4 mesh plus 14 mesh.
Objective – to concentrate the particles of highest metal content (lowest specific gravity).
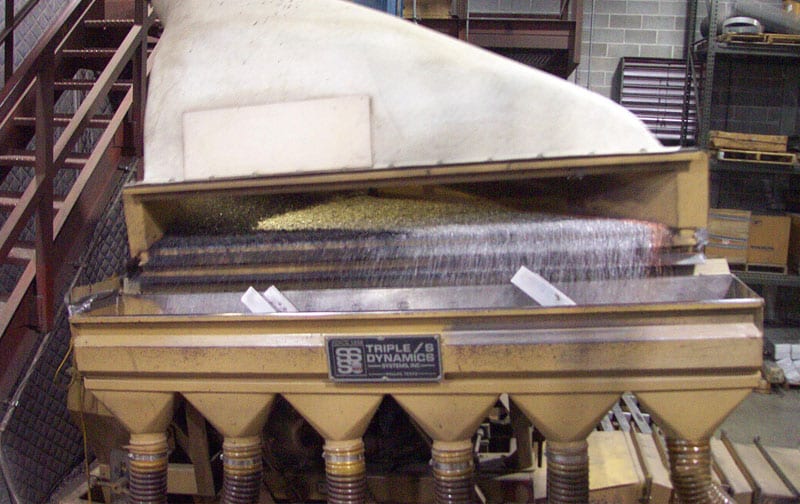
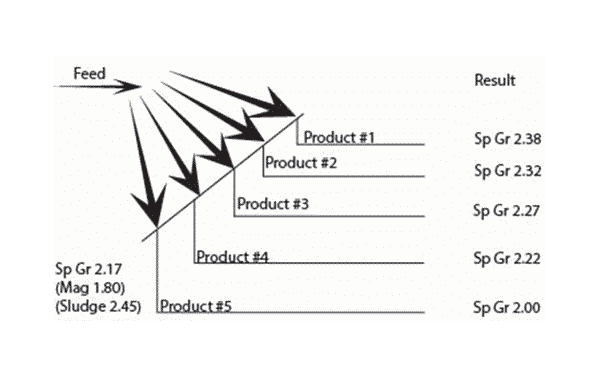