Slipstick Industrial Conveyor for...
Slipstick® Industrial Vibratory Conveyor
Triple/S Dynamics pioneered horizontal motion conveying in the early 1970’s. The first units were sold into foundry and heavy metal operations. The Slipstick’s reliability in these harsh environments is unmatched. Some of the original 1970’s units are still in operation today. The Slipstick® Horizontal Motion Conveyor is recognized for its non-vibratory conveying motion and enviable record of low maintenance, high reliability performance. The slow forward-quick return motion is independent of natural frequency, springs and tuning.
Highly effective for conveying bulk granulator, heavy or powdered products, the Slipstick’s gentle motion practically eliminates dusting and spillage, and wear on the pan is reduced with the lack of vertical, impacting motion.
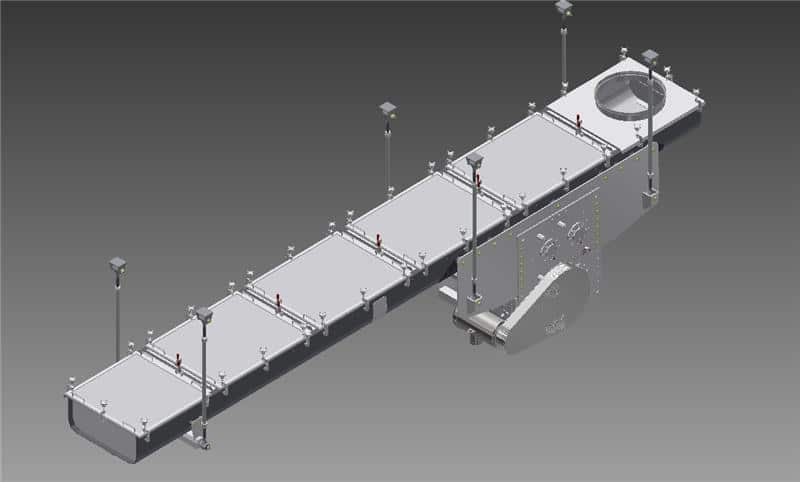
Industrial Vibratory Conveyors
The Slipstick Industrial Conveyor is at work in almost every industry around the globe – any industry that needs vibratory conveyors for bulk material handling.
Form / Function
The key to horizontal motion conveying is the action of the conveyor upon the inertia of the conveyed materials. During the slow advance of the conveyor’s cycle, material is at a relative rest on the conveying surface. The quick return segment of the cycle gently slides the conveying surface under the material bed. Repeating this cycle 200 – 300 times per minute serves to smoothly convey the material over forty feet per minute along the length of the conveying surface. This gliding of the product along the seamless one-piece formed conveyor pan discourages build-up of materials on the surface and typically scours the pan clean so there’s less time required between production cycles for cleaning. At the same time, the horizontal motion conveyor offers a much higher level of mechanical simplicity than either screw or drag conveyors.
This mechanical simplicity offers a conveyor that requires significantly less maintenance. In addition, with no chains, screws, sprockets, rollers, idlers, or other moving parts located outside of the sealed and guarded drive unit, the horizontal motion conveyor is intrinsically safer for operating and maintenance personnel. The reliability can be an order of magnitude above those other types of conveyors as well. Based on its unique design that features a self-contained drive unit that has no outbound moving parts, the horizontal motion conveyor is virtually maintenance-free. And based on its relatively slow rotational speed, a typical drive unit will usually deliver more than ten years of life between service intervals, with only periodic lubrication required. Finally, since these conveyors utilize no springs or counterweights, they do not require the periodic tuning that is part of an ongoing maintenance program for conventional vibrating systems.
This horizontal motion conveyor design offers a number of advantages over conventional vibrating conveyors, belt conveyors, pneumatic conveyors, screw conveyors, and drag conveyors often used in bulk handling applications. Compared to conventional vibrating conveyors, which are usually powered by springs and convey material through the impact on the conveyed material, the horizontal motion conveyor provides gentle transportation, longer lengths, reversibility and many features other types of bulk handing conveyors can’t provide.
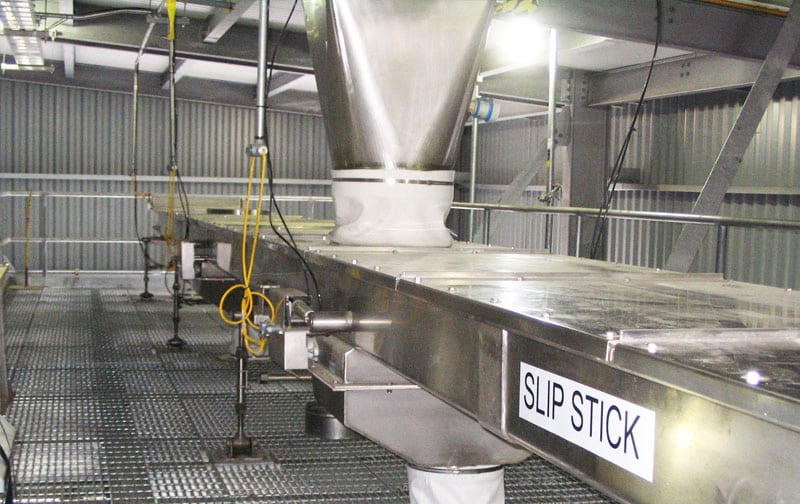
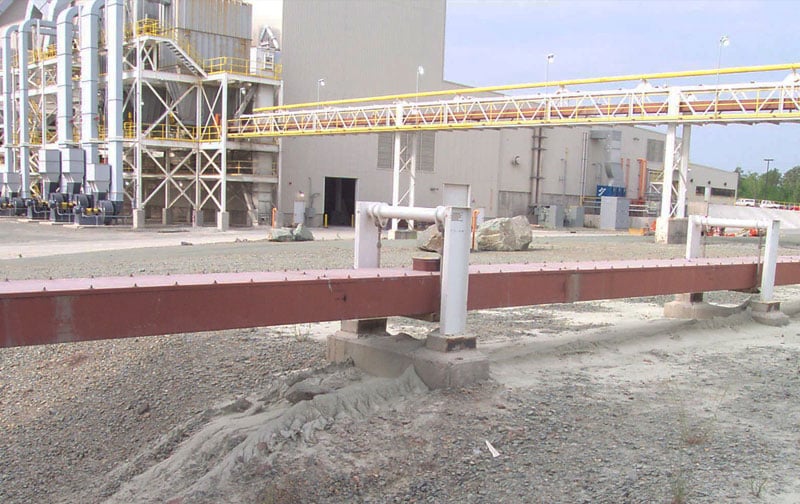
Configurations
Built in lengths from 4 ft to more than 250 ft, the Slipstick offers a variable rate of product delivery depending upon the application, and can be adjusted to suit most any requirement.
The Slipstick can be suspended from overhead to maximize the use of valuable floor space or built with floor-mounted pedestals. More support options are available if existing facility/space/access is an issue. Because it is dynamically self-balancing, no counterweights or heavy isolation bases are necessary. The drive module can be mounted at either end or above/below the conveyor’s pan section. The simple pan with no relative moving parts can be very compact. This allows fitting into tight elevation and width restrictions. In addition, these conveyors can be operated at variable speeds, and their conveying direction is reversible. Conveying surfaces may be carbon, stainless, or abrasion resistant steel, as well as polyethylene plastic, or titanium.
On the larger capacity Slipstick conveyors, structural trusses and impact beds can be incorporated into the design and the conveyor pan is constructed of abrasion-resistant plate metal an inch thick or more. As a result, the conveyor can handle massive impact loads and carrying capacities. One conveyor weighs in at more than 350,000 pounds, pan length of 140 feet long, almost 8 feet wide and 3 feet deep, moving more than 600,000 pounds of scrap steel.
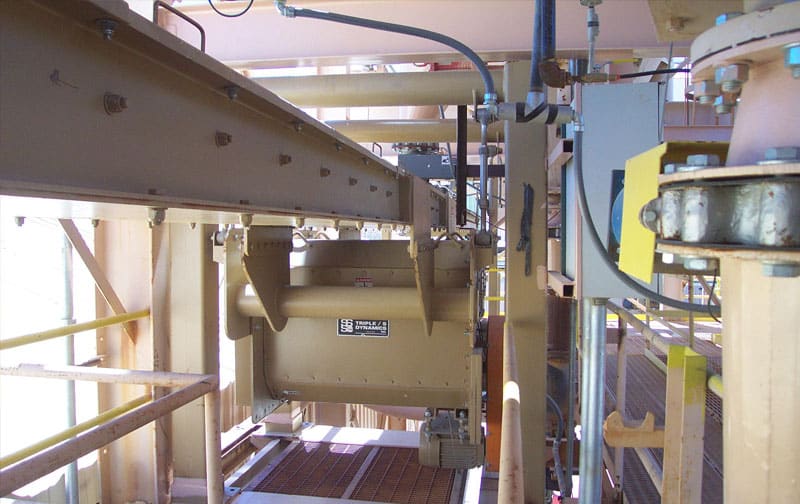
Dust Control
Because the Slipstick Conveyor employs a differential drive and moves materials without moving parts, it is both durable and low maintenance. The product contact pan can be covered with a tight seal that ensures a clean, dust-free environment, and the absence of exposed conveyor parts makes this system one of the safest available.
No fines or dust are generated in Slipstick pan. What is generated from infeed is easily contained with flexible connections and gasketed covers. With no dust generated, expensive dust control systems can be downsized, fewer hours dedicated to clean up, especially important when the material is hazardous. Errant dust from other systems can be cleaned more easily under the simple pan that can be supported from the structure above.
The Slipstick conveyor can also be constructed in a sealed rectangular tube form. This conveyor uses the same gentle slow-advance/quick return motion of the conventional Slipstick to convey materials, coupled with a tightly sealed tubular transport section. With an excellent service history in harsh operating environments, the Slipstick Conveyor has proven to be a highly effective, cost efficient conveying solution minimizing expensive downtime required for maintenance and can be equipped with discharge gates, inlet and outlet seals, access ports, and available lengths of over 200 feet and capacities of over 200 tons per hour.
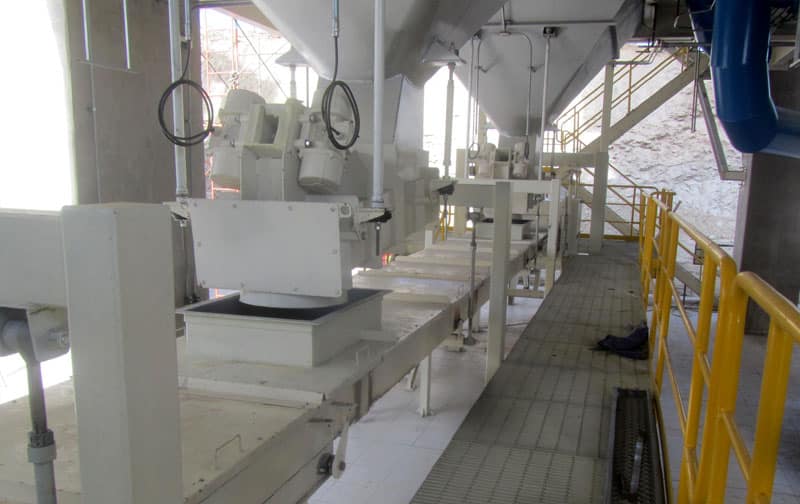
Industrial Applications
Based on its many advantages over conventional vibratory conveyors, the horizontal motion conveyor is increasingly being utilized in a wide range of powder and bulk handling applications. There are a number of demanding applications where the special attributes of the horizontal motion conveyor can be significant including:
- Crushed ores: the combination of abrasion-resistant pans, the ability to accommodate large, heavy volumes, and thorough dust containment characteristics make horizontal motion conveyors a practical choice for this demanding application.
- High temperature materials: with no springs to fail, the horizontal motion conveyor can operate in a wide range of extreme temperatures. In certain applications, air or water cooling systems have been used with horizontal motion conveyors to reliably handle materials up to 1700 F.
- Pharmaceuticals: because the horizontal motion of these conveyors naturally eliminates product sticking and the creation of fines and other residual materials, they are ideally suited to meeting the most demanding requirements of sanitation and cleanability.
- Hazardous or toxic materials: based on the total isolation of conveyed material that can be achieved with enclosed horizontal motion tube conveyors, hazardous and/or toxic materials can be transported without fear of escaping fugitive dust/fumes.
Other applications currently using Slipstick Conveyors include:
- Ash
- Activated Carbon
- Barium Sulfate
- Calcium Carbonate
- Calcium Oxide
- Carbide
- Carbon Black
- Cat Iron
- Catalyst
- Cement Clinker
- Ceramics
- Detergents
- Dextrose
- Granite
- Hydrocarbon Resin
- Paper
- Resin
- Phenolics
- Plastic Pellets
Options
- Materials of
Construction - Wear resistance
- Low profile pans
- Impact liners
- Sealed environment
- Corrosion resistance
- Dual direction
- Distribution options;
Gates - Heating/Cooling
Chambers - Supports
- Product dams
- Multi-lane
- Textured pans
- Chutes
- Flow Inhibitors
- Platforms
- Non-metallic sections
- Non-Ferrous sections
- Grizzly Sections
- Metering
- Dewatering
- Cooling
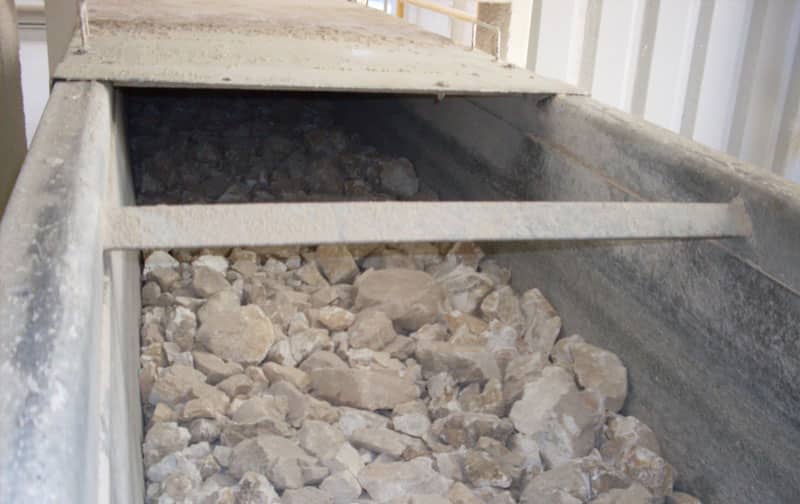
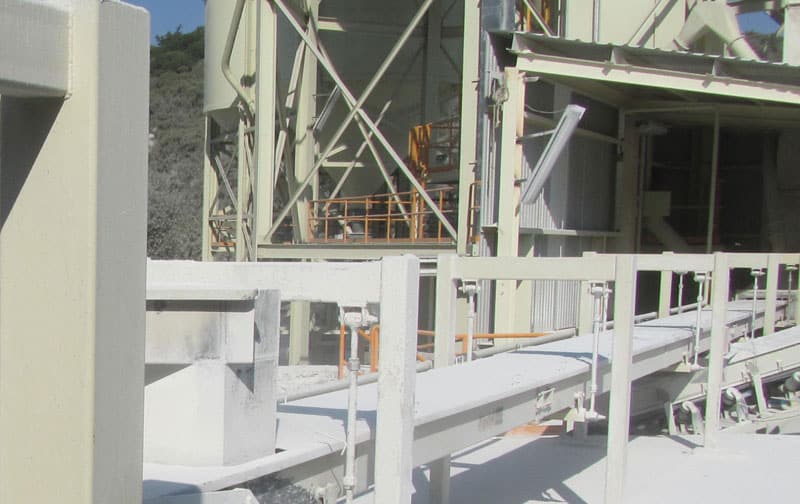
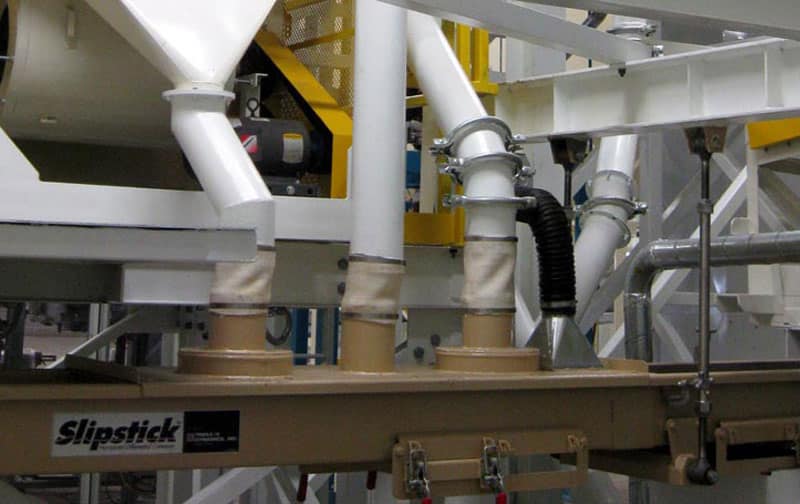
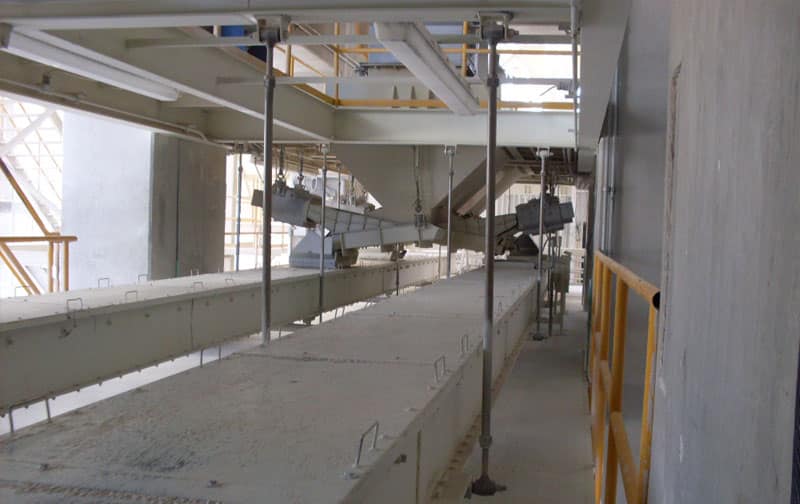